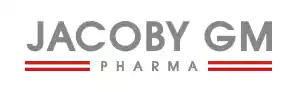
By simplifying warehouse processes at its six locations, Jacoby GM Pharma has significantly increased transparency and reduced the error rate in order picking from 1.6 to 0.5 per mille. In addition, the privately held company has rolled out new hardware from Zebra to enable compliance with the requirements of the EU Falsified Medicines Directive (FMD).
Challenge:
- Six locations with different warehouse processes.
- Little transparency regarding order picking status.
- FMD requires new scanners and processes.
Solution:
- ZetesMedea Logistics Execution Solution.
Results:
- Compliance with FMD.
- Order picking error rate reduced from 1.6 to 0.5 per mille.
- Manual entry eliminated.
- Higher customer and employee satisfaction.
- Simplified administration.
- Maximum transparency for all goods movements.
- Process tracking and traceable order picking operations.
- 2D scanners made possible.
Three companies, six locations: The Austrian pharmaceutical wholesaler Jacoby Pharma GM was created by the merger in 2013 and 2015 of the privately held companies Jacoby Pharmazeutika, GM Pharma and Kögl Pharma. The two-stage merger resulted in a powerful supplier with a leading market position in western Austria. However, there are different standards and warehouse processes in the six associated warehouse and logistics locations, which only partially work with digital data acquisition devices.
Proven sources
“Given the situation, in 2018 we were looking for a software solution to optimise our processes at all branches and standardise them as much as possible", recalls project manager Andreas Trentinaglia, IT Manager at the Innsbruck location. Another aim of the investment was to ensure compliance with the EU Falsified Medicines Directive (FMD) (see inset). It specifies that every selling unit must have a unique, serial number that is stored in an official database along with the product data. This number, which can contain up to 20 digits, is printed on the labelling of the selling unit in the form of a 2D data matrix barcode. “However, previously our scanners were only suitable for 1D barcodes”, says Franz Petrak, authorised officer and Head of Logistics and IT at the Braunau location.
With regard to hardware, Jacoby GM has been using Zebra data capture devices from Zetes Austria since 2009. “Our experience with Zetes and Zebra has been good, so we also wanted to use these proven sources for the new generation of scanners”, notes Trentinaglia, who together with his team opted for the TC8000 mobile touch computer and the WT6000 wearable computer together with type RS5000 ring scanners. The screen of the TC8000 faces the user even during scanning, so the devices does not have to be flipped for each scan operation. This increases the efficiency of each scan.
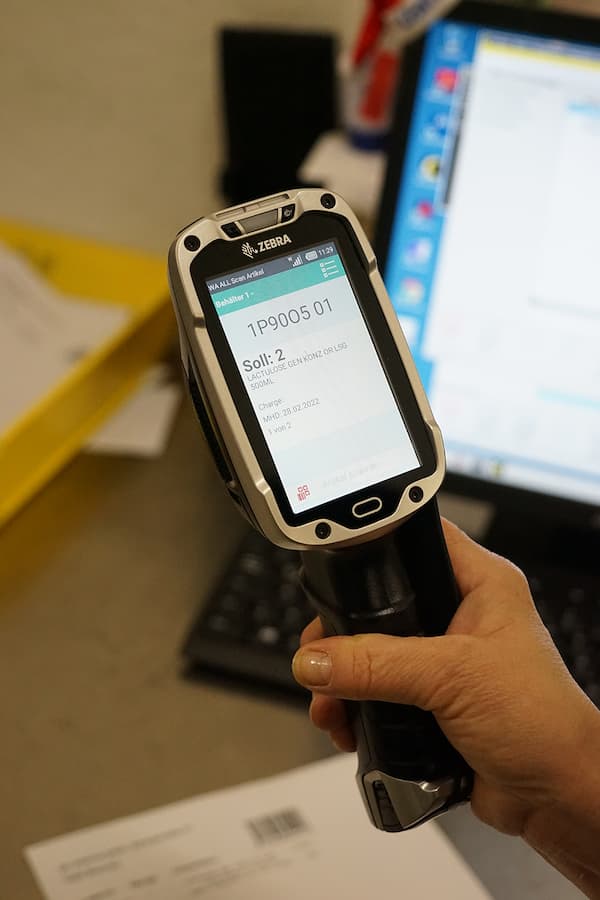
Reliable guidance
During the initial project to replace the hardware, Zetes Solution experts also identified efficiencies that could be gained through more streamlined processes within the warehouse. The pharmaceutical wholesaler was especially interested in the ZetesMedea warehouse execution system (WES). “ZetesMedea impressed us in particular by how quickly it could be incorporated in our IT landscape”, says Trentinaglia. ZetesMedea can exchange order and stock data with the ERP system developed by Jacoby, and it can control and digitise all processes from goods receiving to shipping. Among other things, this includes goods receiving, storing items, taking stock and order picking. This only requires the mobile devices to be equipped with the ZetesMedea app, after which the pickers can reliably perform the process.
ZetesMedea can also be configured for a wide variety of processes, which cannot be standardised in all six locations. In Hallein, Braunau, Klagenfurt, Salzburg and Hohenems, the order picking containers are mostly transported from one station to the next by truck and filled by a different employee at each station, but the picker-to-goods method is used in Innsbruck. “The warehouse in Innsbruck covers three floors, and due to the building structure, it cannot be automated", explains Trentinaglia. There are four orders processed in parallel by employees travelling from one corridor to the next with an order picking cart. There are also minor differences in the process between the other five locations, which cannot be standardised.
Standardised application
In two joint workshops with employees from Jacoby GM Pharma and Zetes, all processes were defined and standardised as much as possible. “Order splitting is also possible with ZetesMedea, when several order pickers have to work on the same order at peak load times to meet tight time windows”, reports Petrak. A special mode that fundamentally alters the process in the ZetesMedea app was created for Innsbruck.
This allows Jacoby GM Pharma to work with a standardised ZetesMedea app at all locations by simply selected the appropriate mode, with only one central interface to the ERP system. The Zebra terminals equipped with the ZetesMedea app are assigned to their respective locations, so they can be configured easily and conveniently by the IT administrators of Jacoby GM via the ZetesMedea dashboard. This convenience is made possible by the MCL™ mobility platform, a mobile enterprise application platform (MEAP) specifically designed for allocation of supply chain processes.
Central management
The MCL™ mobility platform manages the entire mobile infrastructure as well as the application and device life cycles. It allows mobile applications to be developed, provisioned, executed and managed quickly and independently of the location, the deployed mobile devices or the respective operating system. This was a key factor in enabling Jacoby GM Pharma to complete the rollout of ZetesMedea at the first locations within just a few weeks. “The elapsed time between the start of the project in December 2018 and the go-live at the Innsbruck location was less than four months, including the workshops and the conception phase”, recalls Trentinaglia.
In daily practice, the dashboard is mainly used for device and order management. It provides an overview of all picking orders and their processing status. The warehouse manager can intervene at any time, for example to prioritise urgent orders. In-depth analyses of the available data, processing times and errors can also be performed from the dashboard to further improve the process.
Quick acceptance
After the rollout, the warehouse employees were quickly eager to utilise ZetesMedea. “Although we allow the old system to be used at any time as a backup solution, after a short while our employees voluntarily decide to switch to ZetesMedea”, reports Petrak. “The graphic user guidance on the displays of the mobile terminals and elimination of manual entries led to quick acceptance”, confirms Trentinaglia. The significant drop in the error rate, which was already at a low level at Jacoby GM Pharma, also testifies to the high ease of use. “Thanks to ZetesMedea, we were able to reduce the error rate from the range of 1.6 to 2.0 per mille to just 0.5 per mille”, says Trentinaglia.
“ZetesMedea impressed us in particular by how quickly it could be incorporated in our IT landscape” says project manager Andreas Trentinaglia, IT Manager at the Innsbruck location
Conclusion
With ZetesMedea and the high-performance Zebra terminals, Jacoby GM Pharma has largely standardised all processes between goods receiving and shipping and has made order picking more transparent, more user-friendly and more reliable. The next step is digitising the ‘last mile’ in scheduling. The aim is to boost the quality of service in the delivery process with ZetesChronos.
About Jacoby GM Pharma
Jacoby GM Pharma is an Austrian pharmaceutical wholesaler with headquarters in Hallein and branches in Braunau, Klagenfurt, Innsbruck, Salzburg and Hohenems. The privately held company has around 400 employees who process some 170,000 medical product packages daily and an annual turnover of approximately EUR 400 million. Jacoby GM Pharma has its own fleet of 35 vehicles that make deliveries to pharmacies, doctors and veterinarians every day. A warehouse stock of approximately 3 million packages and 30,000 stock items ensures an availability of 99.1 per cent. For more information, visit www.jacoby-gm.at
Background: The EU Falsified Medicines Directive (FMD)
The EU Falsified Medicines Directive (FMD), which came into effect in February 2019, provides for mandatory safety verification of all deployed medical product packaging. Every individual selling unit must have a unique, randomised serial number, which is stored in an official database along with the product data. This number, which can contain up to 20 digits, is printed on the labelling of the selling unit in the form of a 2D GS1 data matrix barcode. The labelling also contains the Global Trading Item Number (GTIN), which is valid worldwide, the expiry date and the batch number.
At every point in the supply chain, the selling unit can be checked for legitimacy by scanning the barcode with a mobile terminal. The mobile terminal contacts the central repository online, checks the authenticity of the serial number, and reads the stored product data. Then the user can immediately verify the authenticity of the product on the display of the mobile terminal.