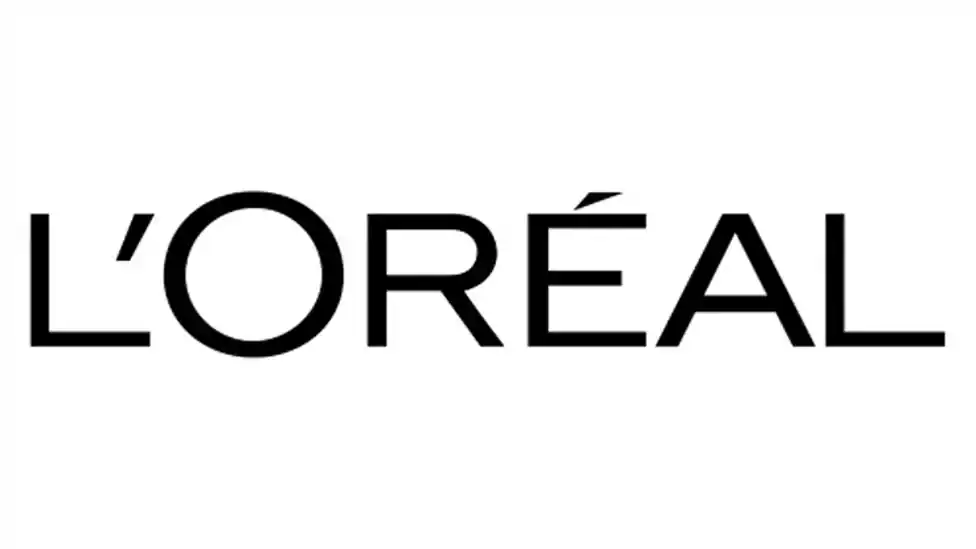
Goods receiving and dispatch operations at L’Oréal’s distribution centre have adopted a Zetes warehouse solution. The system, which uses industrial IND terminals integrated with SAP, has radically improved workplace ergonomics.
Global market leader in beauty products L’Oréal, distributes the L’Oréal Produits de Luxe luxury range from its Nijvel site onto Belgium, The Netherlands, Norway, Denmark and Sweden. Each month, around 4,000 to 4,500 products pass through the hands of sixty staff. In early 2011, the cosmetics giant decided to improve cumbersome and physically demanding operating processes used in the goods receiving and dispatch areas.
Until that time, the goods receipt area used a central, shared label printer. Armed with a Pocket PC, an average of two members of staff were required to continually shuttle back and forth between checked shipments and the printer. In addition, due to their small keypads, the Pocket PCs used were anything but user-friendly, which exacerbated human error levels. Meanwhile, in the goods dispatch area, warehouse attendants used several handheld scanners when readying boxes for dispatch on a conveyor belt. As a result, only one destination could be handled per session. L’Oréal commissioned Zetes to devise a solution to radically improve worker ergonomics.
Consulting with warehouse operators for perfect solution
Zetes’ solution was extensively field-tested by warehouse operators and based on their feedback, a solution was honed that fully met the requirements of all parties concerned.
Employees in the goods receiving area were given three height-adjustable parcel trolleys latticed on three sides. Each parcel trolley was mounted on a battery-charged IND terminal with a touch screen and keyboard integrated online with L’Oreal’s central SAP software. In addition, trolleys are equipped with a label printer and wireless barcode scanner, giving operators everything they need to handle products quickly, without errors and all within easy reach.
Inside the goods dispatch area, at the end of six conveyor belts, Zetes set up a height-adjustable support onto which the relevant terminal type has been mounted, making it easy to operate for every employee, both in terms of height and length. Now, just a single scan is needed to prepare a consignment. Moreover, using the terminal allows for several pallets and destinations to be processed simultaneously as a single online session. SAP’s industrial interface guarantees stable mobile data communications and real time synchronisation of screens.
Simpler, swifter & more user-friendly
As a result of using Zetes’ solution, L’Oréal runs simpler, swifter and more user-friendly goods receipt and dispatch operations. The solution has improved process workflow quality and saves time.
L’Oréal’s Nijvel Stock Officer Jacques Capiau concludes, “Zetes is a partner who understands the problems we face and has the know-how to give us the technical support and guidance we need. As ever, they have more than exceeded our expectations.”
Zetes’ products and services have also been implemented at other L’Oréal sites in France and Portugal, where Zetes’ Voice solution is currently in use.