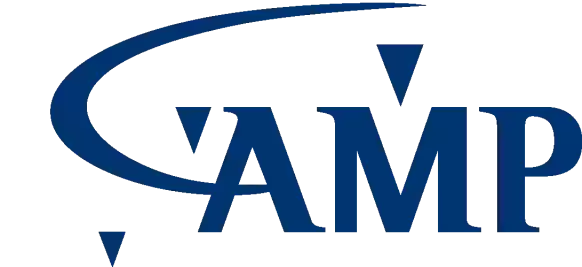
Press distributor AMP successfully integrated a new Proof of Delivery and Proof of Collection system based on two Zetes solutions: ZetesMedea and ZetesChronos.
AMP is part of the French Lagardère group and is regarded to be the market leader in the distribution of magazines and newspapers to newsagents in Belgium. To create a clear real-time overview of the distribution processes, AMP successfully integrated a Proof of Delivery (POD) and Proof of Collection (POC) system based on two Zetes solutions: the ZetesMedea solution facilitates the acceptance and crossdocking of goods in the distribution centres, whilst the ZetesChronos solution optimises the delivery and returns process through POD and POC. Both solutions contribute to informing AMP’s customers of the real-time status of deliveries. In addition, maximum transparency improves correctness and speed of deliveries under time pressure.
AMP’s different distribution centres are geographically dispersed across the country - a strategic choice - to ensure the most efficient delivery of newspapers and magazines to press points of sale (independent newsagents and store chains such as Carrefour, Delhaize, Total...). Every week, 6 nights out of 7, 350 lorries packed with magazines, newspapers and parcels (including those from the Kariboo! network) set off at the crack of dawn to deliver orders to thousands of retail outlets in Belgium. Unsold newspapers and magazines are returned and processed in AMP distribution centres amongst other places.

Full visibility on logistics flows
To guarantee complete transparency in the logistic infrastructure, AMP decided to replace their paper-based operations with a robust delivery tracking system.
AMP eventually opted for a system based on two solutions from the Zetes’ Collaborative Supply Chain portfolio: ZetesMedea increases the operational efficiency of AMP’s distribution centres, whereas ZetesChronos optimises AMP’s POD and POC process.
Zetes’ solution offers a transparent logistic chain between AMP’s distribution centres and thousands of retail outlets. Both the SAP system and packing machines (AERO and HS News) are fully integrated. Moreover, AMP opted for PDAs equipped with a camera, GPS and GPRS.
Acceptance and cross-docking based on barcode scanning
The acceptance and cross-docking flow at AMP is as follows: newspapers and magazines are sorted in the distribution centres per title in totes that have different barcodes. Through an automated sorting system, a customer order is completed by picking newspapers and/or magazines from the different trays. The drivers arrive at the distribution centres during the night and start loading the totes that are ready to be delivered. They receive a list of all the stops that are part of their route. At the same time, the routes and stop information is sent to the ZetesChronos POD application. Also, the return flow is included as unsold newspapers and magazines return to the distribution centre, to be processed and sent back to the publishers.

Efficient Proof of Delivery and Proof of Collection
Aside from the delivery flow to newsagents, the central distribution centre also dispatches to other distribution centres. For example, international newspapers are ordered in limited numbers and stored at the main distribution centre. Each distribution centre has terminals that facilitate the acceptance of goods. Thanks to the back-end application, dispatchers are able to trace different goods.
The drivers’ stops are stored in GPS coordinates on the PDAs which are checked by the route monitor, which also tracks the flow of night time deliveries per distribution centre. Every one to two minutes, the route monitor registers the PDA’s location, allowing the distribution centre to intervene if necessary and providing an overview showing which driver is able to include an extra stop.
At each delivery, photos are taken using the PDA and possible incidents may be reported (e.g. in the event of an unattended delivery). This data will immediately be fed back to the central system.
At the end of their shift, drivers return to the distribution centres where the goods (returns, as well as incomplete goods, for example) will be unloaded and registered.
Meeting reporting requirements (to third parties)
Thanks to Kariboo!, the group’s parcel service which was launched for the Belgian market in February 2014, consumers are now able to send their parcels or have their online orders delivered to more than 600 newsagents and local shops.
Naturally, Kariboo! adheres to stringent service level agreements and oversees that both the end consumer and the company using Kariboo!’s services know at all times where and what the delivery status of the parcel is. All this, thanks to Kariboo!’s new delivery tracking system.
Successful cooperation
Rolf Vermeulen, Operations Director at AMP: “The implementation of our Proof of Delivery solution was originally intended to support our diversification strategy, including the launch of a new parcel service, Kariboo!. Today we cannot live without it. Zetes delivered a complete solution that gives us end-to-end visibility throughout our supply chain and allows us to execute pickups, deliveries and reverse logistics more efficiently”.