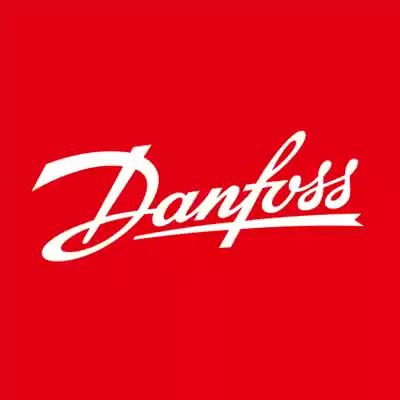
Das im dänischen Nordborg ansässige Unternehmen Danfoss ist weltweit führend in der Entwicklung und Herstellung von energieeffizienten Lösungen mit über 23.000 Beschäftigten und 61 Produktionsbetrieben. Seine Kunden umfassen Privathaushalte bis hin zu Industriebetrieben und Wohnungsbaugesellschaften sowie Partner aus der Industrie aus über 100 Ländern. Das Hauptlager von Danfoss in Roedekro verarbeitet jährlich 1,5 Millionen Auftragspositionen und 80.000 Lieferungen. Täglich kommen dort rund 100 Lkw-Ladungen mit Vorräten an und verlassen das Lager. Diese erfüllen täglich mehr als 350 Lieferungen von Kundenaufträgen an Vertriebspartner an zahlreichen Standorten.
Ziele:
- Verbesserung der Ladepräzision
- Beseitigung von Versandfehlern
- Kürzere Lieferzeiten für die Kunden
- Senkung der Logistikkosten
Lösung:
- ZetesMedea Loading Verification
- ImageID – Automatisierte Bildverarbeitungstechnologie
- ImageBank-Prüfpfad in Echtzeit
Ergebnis:
- Vollständige Amortisierung in zwölf Monaten
- Visueller Versand- und Zustandsnachweis
Null Lieferfehler bedeuten zufriedenere Kunden
Kostspielige Ineffizienz bei der Ladungsprüfung
Danfoss erfüllt strenge Compliance-Verfahren, insbesondere bei Lieferungen außerhalb der Europäischen Union. Der Prüfprozess für die Fahrzeugbeladung war zeitaufwändig und umständlich: Bisher mussten die Paletten in einen Abfahrtbereich gebracht und die Papiere von Hand abgezeichnet werden, bevor die Waren für den Weitertransport aufgeladen werden konnten.
Wenn sich eine Palette, die innerhalb von Europa versendet werden sollte, an der falschen Stelle im Ladebereich befand, wurde der Betrieb erheblich aufgehalten. Aufgrund des hohen Zeitdrucks verfügte Danfoss nur über ein sehr kurzes Zeitfenster, in dem geprüft werden musste, dass die europaweiten Lieferungen auf das richtige Fahrzeug geladen wurden. Die Folge waren häufige von Menschen verursachte Fehler. In einigen Fällen wurden diese jedoch erst erkannt, wenn Danfoss eine entsprechende Meldung von seinen Speditionen erhielt, dass die falschen Waren zum Weitertransport geliefert worden waren.
„In einem Fall schickten wir eine Palette nach Island, die eigentlich nach Italien gehörte – einfach nur, weil wir keinen soliden Prozess hatten, um zu prüfen, dass sich die Palette am richtigen Ort befand, um auf das richtige Fahrzeug geladen zu werden“, erzählt Henrik Rosendahl Laursen, Berater für Lagerwirtschaft und Vertrieb bei Danfoss. Derartige Fehler führten zu erheblichen Unterbrechungen und Problemen, weil die Waren auf Kosten von Danfoss an das Lager zurückgebracht werden mussten; danach mussten die richtigen Waren abgefertigt werden und manchmal führte dies auch zu Verspätungen bei der Lieferung an den Kunden.
„Es lässt sich nur schwer sagen, wie oft Fehler beim Beladen der Fahrzeuge auftraten, aber wir können gut und gerne von rund 600 Paletten/Kisten pro Jahr ausgehen“, schätzt Henrik Rosendahl Laursen. „In den schlimmsten Fällen mussten wir die richtigen Waren hinterher per Luftfracht versenden, um den Zeitverlust wieder aufzuholen. Natürlich müssen wir auch die Kosten im Blick haben, aber die Zufriedenheit des Kunden war noch wichtiger.“
Mehr Personal oder Automatisierung?
Diese Probleme waren der Auslöser dafür, dass Danfoss eine Lösung suchte, um die Präzision beim Beladen der Fahrzeuge zu verbessern, Lieferfehler zu vermeiden und zugleich die Produktivität zu steigern. Das Unternehmen überlegte, ob es mehr Personal für das Lager beschaffen sollte, um alle Lieferungen physisch zu überprüfen, oder ob stattdessen eher eine Technologielösung für die Ladungsprüfung in Frage kam. „Angesichts der Frage, ob wir mehr Personal zur Verbesserung des Prozesses einstellen sollten, hatten wir vor allem Bedenken, ob der Ladeprozess dadurch zuverlässig genug würde, um die hohen Arbeitskosten auszugleichen“, erklärt Henrik Rosendahl Laursen. Außerdem war klar, dass Danfoss bei Implementierung einer Technologielösung jedes Mal von einem zuverlässigen, konsistenten Prozess und zuverlässigen, konsistenten Ergebnissen profitieren konnte und dass dies auch äußerst wertvoll für das Benchmarking der künftigen Präzisions- und Produktivitätsraten sein könnte.
Das Unternehmen entschied sich für eine automatisierte Lösung zur Optimierung der Präzision bei der Ladungsprüfung und beim Versand. Es erkundigte sich bei zahlreichen Anbietern, holte Empfehlungen von vergleichbaren Transportdienstleistern in Dänemark ein und stellte fest, dass die meisten Unternehmen eine maßgeschneiderte Lösung verwenden. Danfoss suchte hingegen eine bewährte, standardisierte und wirtschaftliche Lösung, die auch die Tür für künftige Upgrades und Produktverbesserungen offen ließ.
Ladungsprüfung mit automatisierter Bildverarbeitungstechnologie
Das Unternehmen fand die Ladungsprüfungslösung ZetesMedea auf der Basis der automatisierten Bildverarbeitungstechnologie ImageID für seine Zwecke am sinnvollsten und praktikabelsten. Die automatisierte Lösung verwendet die maschinelle Bildverarbeitung auf der Grundlage der Datenerfassung. Sie analysiert und erfasst Palettenetiketten automatisch in Sekundenschnelle. Die Lösung wurde in das WMS bzw. ERP-System von Danfoss integriert. An jeder Verladerampe wurde eine 5-Megapixel-Kamera installiert. Mit dieser erfasst und liest das System sofort die Barcodeetiketten der Paletten, vergleicht diese mit den Versandinformationen und gibt dem Bediener ein Signal – entweder grünes oder rotes Licht – zur Weiterverarbeitung. Außerdem nimmt sie Bilder von jeder Palette, jedem Rollcontainer oder jeder Kiste auf und speichert diese in einer speziellen Bilddatenbank (ImageBank), um unwiderlegbar nachzuweisen, dass der Auftrag korrekt geladen und versandt wurde.
Die Implementierung begann im Jahr 2015 mit einem ersten Piloten an einer Verladerampe. Nachdem der Prozess ausgefeilt war, wurde das System auf alle 14 Verladerampenbereiche ausgeweitet.
Das Projekt dauerte 6 Monate. Dieser Zeitrahmen ergab sich aus der Notwendigkeit von Danfoss, die eigenen präzisen Lösungsanforderungen zu definieren, die vorhandenen Abfertigungsprozesse neu auszurichten, neue Etiketten herzustellen, den Zugang auf spezifische Dokumentationen an der Verladerampe sicherzustellen und sich so aufzustellen, dass etwaige Änderungen mit entsprechender Gewissheit genehmigt werden konnten.
Wichtigste Vorteile
Bilder als Nachweis
„Es wurde schnell deutlich, dass die Ladungsprüfungslösung ZetesMedea der ideale Ansatz war, weil sie die Waren beim Passieren des Laderampentores automatisch überprüft und einen visuellen Nachweis liefert, mit dem wir genau nachprüfen können, was abgefertigt wurde. Bei Reklamationen von Kunden dient uns das Foto als Nachweis, und wir sind dabei, einen sehr praktischen Prüfpfad mit unserer wachsenden Versanddatenbibliothek zu erstellen“, erklärt Henrik Rosendahl Laursen.
Transparente Betriebsabläufe
Das System ist in die WMS-Lösung von Danfoss integriert. Dadurch kann die Geschäftsleitung den Betrieb an der Laderampe jederzeit einsehen. Fehler werden schnell identifiziert und behoben.
Null Fehler
Die Zetes Lösung kann Paletten mit einer Höhe von bis zu zwei Meter einscannen. "Seit der Einführung vor 10 Monaten haben wir überhaupt keine Ladefehler mehr verzeichnet. Das System warnt uns, wenn ein Fahrer die falschen Paletten auf seinen Lkw lädt. Insgesamt war es ein aufregendes Jahr mit erheblichen qualitativen Verbesserungen.“
Amortisierung in zwölf Monaten
Bei den ursprünglichen Planungen zu diesem Projekt rechnete Danfoss damit, dass sich die Investition innerhalb von zwei Jahren amortisieren würde. Diese Prognose wurde nun dank der überwältigenden Ergebnisse in der Anfangsphase des Projekts auf zwölf Monate herunterkorrigiert. „Wir erfassen mehr Irrtümer und Ladefehler als ursprünglich geschätzt, weil wir andere Phasen im Prozess außerhalb der Beladerampe identifiziert haben, in denen Fehler verursacht wurden. Nun können wir die Beseitigung dieser Fehler ebenfalls angehen“, erklärt Henrik Rosendahl Laursen. „Beispielsweise führten Systemfehler, durch die ein falscher Zielort angegeben wurde, dazu, dass ein Karton auf der falschen Palette landete.“
Präzisere Zeitplanung
Eine präzisere Zeitplanung wurde ermöglicht, und Danfoss kann seine Versandzeitpläne jetzt genauer verwalten, um sich auf die spezifischen Anforderungen der Kunden einzustellen. Früher waren spezielle Auftragswünsche nicht sichtbar, wenn ein Kunde die Lieferung von Waren für einen bestimmten Tag anforderte, und es gab keinen Mechanismus, um zu kontrollieren, ob die Waren zu früh versandt wurden. Die Aufträge wurden ohne Informationen an die Verladerampe übermittelt, und die Bediener versandten die Waren einfach, sobald diese im Lager verfügbar waren, unabhängig von etwaigen Terminwünschen der Kunden. „Heute wird eine Fehlermeldung ausgelöst, wenn eine Palette zu früh für die Abfertigung verladen wird, und der Prozess wird angehalten. Dadurch können wir sicherstellen, dass die Waren termingerecht an den Kunden versandt werden. Unsere Kunden sind seitdem viel zufriedener.“
Gleichzeitiges Beladen von Lkws
Neben der Beseitigung von Fehlern wurde auch die Effizienz verbessert. Denn obwohl das Beladen immer noch genau so lange dauert wie vorher, können die Bediener jetzt mehrere Lkws gleichzeitig fehlerfrei beladen. Dies bietet einen zusätzlichen Vorteil, weil Danfoss das Lagerpersonal dadurch flexibler planen und je nach den täglichen Prioritäten für andere Aufgaben einsetzen kann. Der Lagerdurchsatz wird dadurch gleichmäßiger. Außerdem haben die Mitarbeiter dadurch abwechslungsreichere Aufgaben und lernen den gesamten Lagerbetrieb besser kennen.
„Jedes Mal, wenn wir einen Fehler aufdecken, bedeutet dies, dass der Kunde die richtigen Waren zur rechten Zeit erhält. Dadurch sind unsere Kunden zufriedener. Früher haben wir von Fehlern erst erfahren, wenn unsere Speditionen die Abweichung meldeten, aber heute entdecken wir unsere Fehler bereits im Ladungsprüfungsprozess. Wir erhalten exzellente Rückmeldungen von den Speditionen, weil sie die Waren in den einzelnen Lieferungen anhand der Bildaufnahme jeder Lieferung einfacher finden können“, berichtet Henrik Rosendahl Laursen.
Seit der Implementierung der Ladungsprüfungslösung ZetesMedea hat Danfoss seinen automatisierten Ansatz bei anderen Unternehmen vorgeführt und sehr positive Rückmeldungen erhalten. „Die anderen Unternehmen in unserer Branche sind sehr beeindruckt von unseren Fähigkeiten und dem Tempo, mit dem wir Aufträge jetzt zur Abfertigung verarbeiten und hundertprozentig fehlerfrei ausführen können, weil alle Fehler an der Ladestelle beseitigt wurden“, erklärt Henrik Rosendahl Laursen. „Ich denke, dass die Lösung für viele Unternehmen hilfreich sein könnte. Wir erwägen auch Möglichkeiten, die Nutzung der Lösung auf unsere anderen Lager auszuweiten und den Prozess weiter zu optimieren, indem wir unsere Dokumentation vereinfachen und rationalisieren.“
Seit Einführung haben wir keinerlei Ladefehler mehr. Das System warnt uns, wenn ein Fahrer falsche Paletten auf seinen Lkw lädt.
Henrik Rosendahl Laursen, Danfoss.