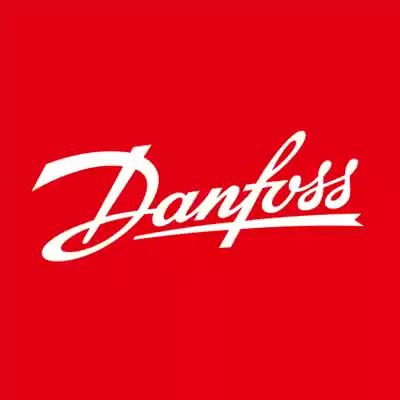
Danfoss, azienda danese con sede a Nordborg, è leader mondiale nello sviluppo e produzione di soluzioni ad alta efficienza energetica, con un organico di oltre 23.000 dipendenti suddivisi in 61 stabilimenti. Tra i suoi clienti annovera singole abitazioni, impianti industriali, imprenditori immobiliari e partner industriali distribuiti in oltre 100 paesi. Il principale magazzino Danfoss, ubicato a Roedekro in Danimarca, gestisce ogni anno 1,5 milioni di righe d'ordine e 80.000 consegne. Ogni giorno partono e arrivano circa 100 camion di prodotti per soddisfare le necessità quotidiane di oltre 350 clienti e destinati ai partner di distribuzione in numerose località.
Obiettivo:
- Migliorare la precisione di carico
- Eliminare gli errori di spedizione
- Ridurre i tempi di preparazione delle spedizioni del cliente
- Ridurre i costi logistici
Soluzione:
- ZetesMedea per la verifica del caricamento
- ImageID - Tecnologia di visione artificiale
- Database delle immagini per il controllo in tempo reale
Risultato:
- Rientro dell'investimento in 12 mesi
- Prova visiva dell'avvenuto caricamento e dello stato della merce
- L'assenza di errori di spedizione si traduce una maggiore soddisfazione del cliente
Il costo di una verifica del caricamento inefficiente
Danfoss rispetta rigorose procedure di conformità, in particolare nel caso di spedizioni di destinate a paesi al di fuori dell'Unione Europea. Il processo di verifica del caricamento era dispendioso in termini di tempo e prevedeva lo spostamento dei pallet in un'area di spedizione, con il controllo manuale della documentazione prima di poter caricare i prodotti per il successivo trasporto.
Se un pallet destinato a un paese europeo veniva posizionato per errore nel punto sbagliato dell'area di carico ne conseguivano gravi disagi in termini di operatività. A causa dei tempi ristretti, Danfoss disponeva di una finestra temporale molto breve in cui verificare che i prodotti diretti ai paesi europei fossero caricati sul veicolo corretto. Di conseguenza si verificavano diversi errori umani e, in alcuni casi, i problemi venivano identificati solo dopo una segnalazione dello spedizioniere che aveva ricevuto la merce sbagliata.
"In un caso abbiamo spedito in Islanda un pallet destinato all'Italia, semplicemente perché non disponevamo di un robusto processo di verifica per controllare che il pallet fosse nel posto giusto per essere caricato sul camion corretto", afferma Henrik Rosendahl Laursen, Warehouse and Distribution Consultant di Danfoss. Errori come questo possono determinare gravi disagi e inconvenienti poiché i prodotti devono essere successivamente riportati al magazzino a spese di Danfoss, con la necessità di inviare poi gli articoli corretti, cosa che spesso comporta ritardi nelle consegne ai clienti.
"È difficile quantificare quante volte si siano verificati errori di caricamento, ma si può ragionevolmente stimare circa 600 pallet/cartoni all'anno", chiarisce Henrik Rosendahl Laursen. "Nel peggiore dei casi può essere necessario trasportare per via aerea i prodotti corretti per recuperare il tempo perso e sebbene la gestione dei costi sia importante, risulta più critico assicurare la soddisfazione del cliente".
Manodopera extra o automazione?
Questi problemi hanno spinto Danfoss a risolvere le difficoltà in termini di accuratezza del caricamento per eliminare gli errori di spedizione e al tempo stesso migliorare la produttività. L'azienda ha valutato se fosse opportuno assumere altro personale di magazzino per controllare fisicamente le spedizioni o adottare una soluzione tecnologica per affrontare il problema. "La principale preoccupazione, qualora si fosse scelto di impiegare manodopera extra, era garantire una sufficiente affidabilità del caricamento, dati gli alti costi della manodopera", spiega Henrik Rosendahl Laursen. D'altro canto una soluzione tecnologica avrebbe permesso a Danfoss di contare su un processo affidabile e coerente, con inoltre notevoli vantaggi futuri in termini di accuratezza e produttività.
La logica conclusione è stata la scelta di una soluzione automatizzata per migliorare l'accuratezza in fase di verifica del caricamento e di spedizione. Per questo Danfoss ha valutato numerosi fornitori, richiedendo inoltre la consulenza di fornitori di servizi di trasporto simili in Danimarca. Il risultato ha evidenziato che la maggior parte delle aziende aveva adottato un approccio personalizzato. Danfoss cercava tuttavia una soluzione collaudata, standardizzata e commercialmente praticabile che tenesse conto di eventuali futuri ampliamenti e miglioramenti dei prodotti.
Verifica del caricamento con la tecnologia di visione
A conclusione delle valutazioni, la soluzione ZetesMedea di verifica del caricamento, basata sulla tecnologia di visione artificiale ImageID risultò la più valida e fattibile per questa applicazione. La soluzione automatizzata utilizza i dati acquisiti dal sistema di visione artificiale per rilevare e analizzare in pochi secondi le etichette dei pallet. Integrata nel sistema di gestione del magazzino o ERP e dotata di videocamere da 5 megapixel installate presso ciascuna banchina di carico, la soluzione permette di rilevare e leggere istantaneamente le etichette con codice a barre dei pallet, confrontando i dati con le informazioni di spedizione per rilevare eventuali discrepanze e inviare un segnale passa/non passa all'operatore. Per ogni pallet, roll-carrier o cassa vengono inoltre scattate immagini, che sono registrate in un database dedicato e rappresentano una prova inconfutabile del caricamento corretto dell'ordine e della sua spedizione.
L'implementazione ha avuto inizio nel 2015 con un progetto pilota su una banchina di carico; successivamente, dopo le necessarie modifiche del processo, è stato ampliato a tutte e 14 le aree di carico.
Il completamento del progetto ha richiesto sei mesi e in questo arco di tempo Danfoss ha definito con precisione i requisiti della soluzione, riallineando i processi di consegna esistenti, predisponendo nuove etichette e rendendo disponibile documentazione specifica presso le banchine di carico per approvare con certezza ogni modifica.
Vantaggi chiave
Immagini come prova dell'avvenuto processo
"È risultato immediatamente evidente che la soluzione di verifica del caricamento ZetesMedea costituiva l'approccio ideale in quanto avrebbe consentito di controllare automaticamente i prodotti lungo il tragitto fino alla banchina di carico, fornendo un riscontro visivo di quanto era stato esattamente spedito. In caso di reclamo del cliente, abbiamo potuto utilizzare le prove fotografiche: un sistema di controllo molto utile basato su un database di dati di spedizione in continua crescita", rivela Henrik Rosendahl Laursen.
Visibilità dei processi
Il sistema è stato integrato nella soluzione di gestione del magazzino Danfoss per garantire la necessaria visibilità sulle attività svolte presso le banchine di carico, con possibilità di identificare e correggere rapidamente eventuali errori.
Zero errori
Il sistema è in grado di eseguire la scansione di pallet alti fino a due metri. Nei 10 mesi da quando abbiamo iniziato a usare la soluzione non si sono verificati errori poiché il sistema segnalava ogni tentativo di un autista di caricare i pallet sbagliati sul proprio veicolo. Nel complesso, abbiamo riscontrato un eccezionale aumento della qualità in un solo anno".
Rientro dei costi in 12 mesi
In fase di definizione dell'ambito del progetto, Danfoss prevedeva di recuperare completamente l'investimento entro due anni, tuttavia gli eccezionali risultati conseguiti hanno consentito di ridurre questo arco di tempo a soli 12 mesi. "Stiamo individuando più errori di caricamento di quanto inizialmente stimato poiché abbiamo identificato altre fasi del processo a monte dell'area di carico in cui si verificano disguidi e stiamo lavorando per eliminare anche questi", spiega Henrik Rosendahl Laursen. "Ad esempio, errori di sistema con indicazione di una destinazione non corretta determinavano il collocamento sui pallet di scatole non corrette."
Pianificazione più accurata
Anche l'accuratezza di pianificazione è stata migliorata e Danfoss può oggi pianificare con una maggiore precisione per soddisfare al meglio le specifiche esigenze dei clienti. In passato, se un cliente richiedeva la consegna di prodotti in un giorno specifico, non era possibile visualizzare questa speciale richiesta inserita nell'ordine e non vi era alcun meccanismo per controllare che i prodotti non fossero spediti troppo presto. Gli ordini venivano inviati alla banchina di carico senza informazioni e gli operatori li spedivano il più rapidamente possibile, a condizione che fossero disponibili a magazzino, senza considerare le tempistiche richieste. "Oggi se un pallet è caricato per essere spedito troppo presto, viene generato un messaggio di errore che arresta il processo. In questo modo possiamo garantire che i prodotti vengano spediti secondo le precise indicazioni fornite, il che fa la differenza in termini di soddisfazione dei clienti".
Caricamento simultaneo di più veicoli
Oltre ad eliminare gli errori, il sistema ha permesso di migliorare anche l'efficienza: sebbene i tempi di caricamento siano gli stessi disponibili in passato, gli operatori sono ora in grado di caricare più veicoli contemporaneamente, senza commettere errori. Si tratta di un notevole passo avanti che ha permesso a Danfoss di impiegare il personale di magazzino in modo più flessibile, organizzando gli operatori in base alle priorità quotidiane. Oltre a rendere più costante la capacità produttiva, ciò ha permesso ai dipendenti di svolgere più compiti lavorativi, maturando così una migliore comprensione dei processi di magazzino.
"Ogni volta che individuiamo un errore significa che il cliente otterrà i prodotti giusti al momento giusto e che stiamo migliorando la soddisfazione del cliente. In passato avremmo ricevuto la segnalazione degli errori da parte dello spedizioniere con una notifica di deviazione, mentre ora siamo in grado di rilevarli autonomamente durante il processo di verifica di caricamento. Riceviamo ottimi feedback dagli spedizionieri poiché l'immagine acquisita rende più facile rintracciare i prodotti in ogni spedizione", spiega Henrik Rosendahl Laursen.
Dall'implementazione della soluzione di verifica del caricamento ZetesMedea, Danfoss ha dimostrato la validità del suo approccio automatizzato ad altre aziende, ricevendo feedback molto positivi. "I nostri colleghi del settore sono rimasti molto colpiti dalle nostre capacità e dalla velocità con cui oggi possiamo evadere gli ordini con un'accuratezza del 100%, in quanto gli eventuali errori vengono eliminati nel punto di carico", dichiara Henrik Rosendahl Laursen. "Ritengo che molte aziende potrebbero trarre vantaggio da questa soluzione e stiamo valutando come estenderne l'utilizzo ai restanti magazzini per migliorare ulteriormente il processo, rendendo i nostri documenti più semplici e facili da gestire".
Da quando abbiamo iniziato a usare la soluzione non si sono verificati errori poiché il sistema segnalava ogni tentativo di un autista di caricare i pallet sbagliati sul proprio veicolo. Henrik Rosendahl Laursen, Warehouse and Distribution Consultant per Danfoss.