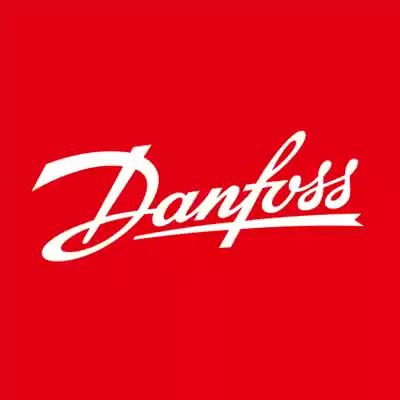
Firma Danfoss se sídlem v Nordborgu v Dánsku je globálním lídrem v oblasti vývoje a výroby energeticky efektivních řešení s více než 23 000 zaměstnanci a 61 továren. Firma má širokou škálu zákazníků od jednotlivých majitelů bytů a nemovitostí až po developery a průmyslové podniky, a dodává svoje produkty do více než 100 zemí. Hlavní sklad firmy Danfoss v Roedekro zpracovává 1,5 milionu objednaných položek a 80 000 dodávek ročně. Každý den sem přijede a odjede přibližně 100 nákladních vozů s obsahem 350 dodávek určených pro distribuční partnery na mnoha různých místech.
Cíl:
- Zvýšit přesnost nakládky
- Vyloučit chyby v dodávkách
- Zkrátit dobu zpracování dodávky pro zákazníky
- Snížit náklady na logistiku
Řešení:
- Ověření nakládky ZetesMedea
- Technologie ImageID Vision
- Databáze auditních záznamů ImageBank v reálném čase
Výsledek:
- Plná návratnost investice během 12 měsíců
- Vizuální doklad nakládky a stavu dodávky
- Bezchybné dodávky zvyšují spokojenost zákazníků
Cena za neefektivní ověřování nakládky
Firma Danfoss musí dodržovat přísné předpisy a standardní procesy, zvláště při zpracování dodávek určených mimo Evropskou unii. Proces ověřování nakládky vozidel byl časově náročný a před nakládkou musely být palety převezeny do výstupní oblasti a bylo nutné ručně zkontrolovat všechny tištěné dokumenty.
Pokud byla některá paleta určená do evropských zemí umístěna na nesprávné místo nakládkové oblasti, vedlo to k závažnému narušení provozu. Vzhledem ke krátké době vyhrazené na zpracování, měli pracovníci firmy Danfoss jen málo času na ověření, zda jsou evropské dodávky nakládány do správného vozidla. Následkem toho často docházelo k chybám lidského faktoru, které byly v některých případech zjištěny až poté, co na ně firmu Danfoss upozornily přepravní služby.
„V jednom případě jsme dokonce odeslali na Island paletu určenou do Itálie, protože jsme neměli dostatečně robustní procesy ověřování, které by zkontrolovaly, zda je daná paleta na správném místě určeném pro nakládku do správného vozu,“ říká Henrik Rosendahl Laursen, Warehouse and Distribution Consultant ve firmě Danfoss. Podobné chyby mohou vést k vážnému narušení procesů a následným problémům, protože zboží je nutné vrátit do skladu na náklady firmy Danfoss a musí být expedovány správné položky, což někdy vede k opožděné dodávce zákazníkům.
„Je těžké přesně určit, jak často docházelo k chybám při nakládce, ale bezpečný odhad bude přibližně 600 palet/kartonů ročně,“ říká Henrik Rosendahl Laursen. „V těch nejhorších případech jsme byli nuceni zasílat správné zboží letecky, abychom dohnali ztracený čas. Sledování nákladů je důležité ale ještě důležitější je zajistit spokojenost zákazníků.“
Navýšení lidských zdrojů nebo automatizace?
Tyto problémy byly impulsem, který přiměl firmu Danfoss řešit přesnost nakládky vozů s cílem eliminovat chyby v dodávkách a současně zvýšit produktivitu. Firma musela vyhodnotit, zda se vyplatí přijmout další zaměstnance skladů k provádění fyzických kontrol všech dodávek, nebo nasadit technologické řešení a vyřešit problémy s ověřováním nakládky. „Trápilo nás, že pokud bychom nasadili další zaměstnance na zlepšení spolehlivosti nakládky, znamenalo by to vysoké náklady na pracovní síly,“ říká Henrik Rosendahl Laursen. Firma Danfoss navíc pochopila, že pokud nasadí technologicky vyspělé řešení, přinese to další výhody v podobě spolehlivých a konzistentních procesů a výsledků, což může být cenným přínosem k zajištění požadované úrovně přesnosti a produktivity.
Na základě rozhodnutí využít k vylepšení ověřování nakládky a přesnosti expedice automatizované řešení si firma Danfoss udělala průzkum různých dodavatelů a vyhledala doporučení od podobných přepravních firem v Dánsku. Jejich poznatky ukázaly, že většina dodavatelů nabízí řešení vyvíjená na zakázku. Firma Danfoss však hledala osvědčené, standardizované a komerčně životaschopné řešení, se kterým by navíc mohli využívat výhod z budoucích aktualizací a vylepšení produktu.
Ověřování nakládky pomocí technologie ImageID Vision
Firma Daffons došla k závěru, že pro jejich účely je nejvhodnější a nejpraktičtější ověřování nakládky pomocí řešení ZetesMedea využívající technologie ImageID Vision. Toto automatizované řešení rychle detekuje a dekóduje štítky na paletách za pohybu. Řešení je integrováno se systémem WMS nebo ERP a pomocí specializovaných kamer instalovaných na branách okamžitě detekuje a přečte štítek palety s čárovým kódem, porovná jej s informacemi o dodávce a ověří případné nesrovnalosti, načež dá obsluze signál „go/no go“. Současně pořídí snímek každé palety, role či bedny a uloží jej do vyhrazené databáze ImageBank, kde slouží jako nevyvratitelný důkaz o správnosti dodávky a stavu palety v okamžiku odeslání.
Implementace začala v roce 2015 úvodním pilotním projektem pro jednu bránu a po vyladění procesu bylo toto řešení rozšířeno na všech 14 nakládkových doků.
Dokončení celého projektu trvalo 6 měsíců, během kterých musela firma Danfoss definovat své požadavky na přesné řešení, přesměrovat stávající expediční procesy, změnit etikety, zajistit přístup k příslušné dokumentaci u bran a dosáhnout stavu, kdy bude možné všechny změny zavést se stoprocentním výsledkem.
Klíčové přínosy
Snímky jako důkaz
„Rychle se potvrdilo, že řešení ověřování nakládky ZetesMedea bylo ideální volbou, protože dokáže automaticky zkontrolovat zboží během jeho přesunu přes brány nakládkového doku a pořídí vizuální záznam na ověření, co přesně bylo expedováno. V případě stížnosti ze strany zákazníka můžeme použít důkazní snímek a díky naší narůstající databázi dat o dodávkách si budujeme velmi užitečné auditní záznamy,“ říká Henrik Rosendahl Laursen.
Sledovatelnost operací
Systém je integrován s řešením WMS firmy Danfoss, takže management má neustálý přehled o operacích v nakládkovém doku a případné chyby jsou okamžitě zjištěny a napraveny.
Eliminace chyb
Systém umí skenovat palety až do výšky 2 m." Za 10 měsíců od spuštění nedošlo k žádným chybám při nakládce, protože nás systém upozorní, když se řidič pokusí naložit nesprávné palety na vůz. Celkově jsme meziročně zaznamenali obrovské zvýšení kvality.“
Návratnost investice za 12 měsíců
Když firma Danfoss původně plánovala tento projekt, očekávala plnou návratnost investice do dvou let, ale na základě působivých úvodních výsledků nyní svoji prognózu upravila na 12 měsíců. „Daří se nám zachytit více omylů a chyb při nakládce, než jsme původně předpokládali, protože jsme odhalili další zdroje chyb v procesech mimo nakládkové doky a nyní pracujeme i na jejich prevenci,“ říká Henrik Rosendahl Laursen. „Například systémová chyba, kdy bylo zadáno nesprávné cílové místo určení, vedla k nesprávnému zařazení kartonu na paletu."
Přesnější plánování
Zvýšila se také přesnost plánování a firma Danfoss nyní může lépe spravovat časové plány dodávek a pružněji plnit požadavky ze strany zákazníků. Když si v minulosti zákazník objednal zboží s doručením v určitý den, neexistoval přehled ani žádný speciální mechanismus jak zjistit, zda zboží není expedováno příliš brzy. Objednávky byly zaslány do nákladového doku bez potřebných informací o požadovaném datu doručení a operátoři je odeslali hned poté, co bylo požadované zboží na skladě, bez ohledu na požadovaný den dodání. „Nyní, když je paleta naložena k expedici příliš brzy, se v systému zobrazí chybová zpráva a proces je zastaven. Díky tomu můžeme zajistit, že zboží bude dodáno přesně podle požadavků zákazníka, což podstatně zvýšilo spokojenost zákazníků s našimi službami.“
Nakládání více vozů najednou
Kromě vyloučení chyb došlo i k zvýšení efektivity. Přestože fyzická nakládka trvá stejně dlouho jako dříve, operátoři nyní mohou pracovat na nakládce více vozů najednou, aniž by docházelo k chybám. To přináší další výhody, protože to firmě Danfoss umožňuje flexibilněji využívat pracovníky skladu a přidělovat je podle denních priorit. Vedle lepšího vyvážení provozu ve skladu to také znamená, že pracovníci mají rozmanitější úkoly a mohou si rozvíjet lepší chápání skladových operací.
„Každá včas odhalená chyba znamená, že zákazník dostane správné zboží ve správnou dobu, což posiluje spokojenost zákazníků. V minulosti jsme se o chybách často dozvěděli až poté, co nám dopravci zaslali zprávu o nesrovnalostech v dodávce, nyní je můžeme odhalit sami během procesu ověřování nakládky. Dopravci jsou s novým systémem také velmi spokojení, protože díky snímkům každé dodávky snadněji najdou jednotlivé položky,“ říká Henrik Rosendahl Laursen.
Po implementaci řešení ověřování nakládky ZetesMedea firma Danfoss předvedla svůj automatizovaný přístup dalším firmám v této oblasti a sklidila velmi kladnou odezvu. „Naši kolegové v oboru ocenili naše schopnosti a rychlost, se kterou nyní dokážeme zpracovat objednávky k expedici se 100% přesností, protože jakékoli chyby jsou napraveny při nakládce,“ říká Henrik Rosendahl Laursen. „Myslím, že pro mnoho firem by toto řešení bylo přínosem. Sami zvažujeme, jak bychom mohli toto řešení rozšířit i na naše další sklady a pokračovat ve vylepšování procesů a dále zjednodušit zpracování dokumentace.“
Od zavedení do provozu nedošlo k vůbec žádným chybám při nakládce, protože nás systém upozorní, když se řidič pokusí naložit nesprávné palety na vůz. Henrik Rosendahl Laursen, Warehouse and Distribution Consultant, Danfoss.