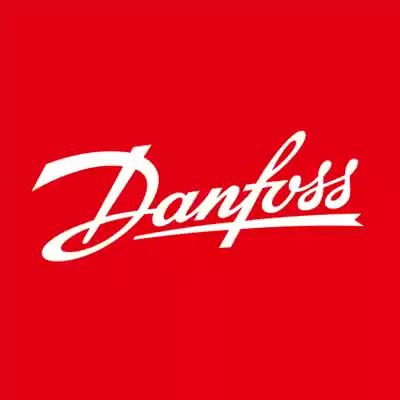
Danfoss, een wereldwijde leider in de ontwikkeling en productie van energie-efficiënte oplossingen, heeft zijn hoofdkantoor in het Deense Nordborg en telt meer dan 23.000 werknemers en 61 fabrieken. Hun klantenkring, die bestaat uit zowel huis- en fabriekseigenaren als vastgoedontwikkelaars en industriële partners, is verspreid over meer dan 100 landen. Het hoofdmagazijn van Danfoss in Roedekro verwerkt 1,5 miljoen bestelde items en 80.000 leveringen per jaar. Elke dag arriveren en vertrekken er zo'n 100 truckladingen met goederen, bestemd voor het leveren van meer dan 350 klantorders per dag, via distributiepartners op tal van locaties.
Doelstellingen:
- Verbeteren van de nauwkeurigheid van het laadproces
- Een einde maken aan verzendfouten
- Kortere doorlooptijden voor zendingen naar klanten
- Logistieke kosten terugbrengen
Oplossingen:
- ZetesMedea Loading Verification
- ImageID - Machine Vision-technologie
- Realtime ImageBank audit trail
Resultaten:
- Volledige ROI binnen 12 maanden
- Visueel bewijs van de lading en de staat ervan
Geen verzendfouten dus meer klantentevredenheid
De tol van inefficiënte laadcontroles
Danfoss moet strenge procedures naleven met name bij het verwerken van zendingen naar bestemmingen buiten de Europese Unie. De voertuiglaadcontrole was een tijdrovend proces waarbij de pallets op een plek voor uitgaande zendingen werden geplaatst en de papieren documenten handmatig afgevinkt werden vooraleer de goederen geladen konden worden voor verder transport.
De werkzaamheden werden ernstig verstoord als een pallet met een Europese bestemming op de verkeerde plek in de laadzone werd geplaatst. Door de krappe en gelimiteerde doorlooptijden had Danfoss maar zeer weinig tijd om te controleren of de zendingen binnen Europa in het juiste voertuig geladen werden. Dit leidde regelmatig tot menselijke fouten, die vaak pas aan het licht kwamen op het moment dat Danfoss geïnformeerd werd door hun externe expediteur dat de verkeerde goederen aangekomen waren voor verdere verzending.
"Het is ooit voorgekomen dat we een pallet verzonden hadden naar IJsland die bestemd was voor Italië omdat we gewoon geen degelijk controleproces hadden om te verifiëren of de pallet op de juiste plek klaarstond om in de juiste truck geladen te worden", vertelt Henrik Rosendahl Laursen, Warehouse & Distribution Consultant bij Danfoss. Fouten als deze leidden tot ernstige verstoringen en veel ergernis omdat de goederen geretourneerd moesten worden naar het magazijn op kosten van Danfoss en de juiste items alsnog verzonden moesten worden met de kans op leveringsvertraging voor de klant.
"Het is moeilijk exact te zeggen hoe vaak voertuiglaadfouten voorkwamen, maar we kunnen gerust stellen dat het om zo'n 600 pallets / dozen per jaar ging", vervolgt Henrik Rosendahl Laursen. "In het slechtste geval moesten we de juiste goederen per luchtvracht verzenden om de verloren tijd in te halen. Het beheersen van de kosten is weliswaar belangrijk, maar klantentevredenheid is nog veel belangrijker."
Extra mankracht of automatisering?
De problemen door fouten hebben ertoe geleid dat Danfoss het correct laden van de voertuigen wilde aanpakken om een einde te maken aan de verzendfouten en tegelijk de productiviteit op te voeren. Het bedrijf evalueerde of ze meer magazijnmedewerkers moesten aannemen om alle zendingen fysiek te controleren of dat ze een technologische oplossing moesten aanschaffen om het laadcontroleprobleem op te lossen. "Gezien de hoge arbeidskosten was de belangrijkste overweging of het inzetten van extra mankracht om het proces te verbeteren het laadproces voldoende betrouwbaar zou maken", zegt Henrik Rosendahl Laursen. Danfoss zag bovendien in dat ze door het implementeren van een technologische oplossing telkens opnieuw verzekerd zouden zijn van een betrouwbaar en consistent proces en resultaat, wat zeer waardevol zou zijn als maatstaf voor het beoordelen van de nauwkeurigheid en productiviteit in de toekomst.
Na hun beslissing om te kiezen voor een geautomatiseerde oplossing voor het verbeteren van de laadcontroles en verzendnauwkeurigheid vergeleek Danfoss verschillende leveranciers en vroegen ze om aanbevelingen bij soortgelijke transportleveranciers in Denemarken. Uit hun bevindingen bleek duidelijk dat het merendeel van de bedrijven gekozen had voor een op maat aangepaste aanpak. Danfoss was echter op zoek naar een bewezen, gestandaardiseerde en commercieel haalbare oplossing die ook garant zou staan voor toekomstige upgrades en productverbeteringen.
Laadcontrole met behulp van machine vision-technologie
Ze kwamen tot de conclusie dat de laadcontrole-oplossing ZetesMedea met de bijbehorende ImageID machine vision-technologie (ook wel Dock Door Control genoemd) het meest rendabel en praktisch was voor het beoogde gebruik. De geautomatiseerde oplossing maakt gebruik van machine vision-based data capture om de palletlabels binnen slechts enkele seconden automatisch te detecteren en te analyseren. Geïntegreerd met een WMS- of ERP-systeem en met een 5-megapixelcamera bij elk laaddock detecteert en leest het direct de barcodelabels op de pallets, controleert het deze op afwijkingen aan de hand van de verzendgegevens en geeft het een 'go/no go'-signaal aan de operator. Er worden ook foto's gemaakt van elke pallet, transportroller en krat, die opgeslagen worden in een speciale ImageBank als onweerlegbaar bewijs dat het order correct geladen en verzonden is.
De implementatie werd gestart in 2015 met een pilot bij één laaddock en toen het proces helemaal op punt stond, werden alle 14 laadplaatsen voorzien.
Het voltooien van het project duurde 6 maanden en in die periode moest Danfoss hun exacte oplossingsvereisten formuleren, hun bestaande verzendprocessen opnieuw afstemmen, nieuwe labels produceren, kunnen beschikken over specifieke documentatie bij het laaddock en elke wijziging met zekerheid kunnen goedkeuren.
Belangrijkste voordelen
Foto's als bewijs
"Het was al heel snel duidelijk dat de laadcontrole-oplossing ZetesMedea de ideale aanpak was omdat deze de goederen automatisch controleert wanneer ze door de poort bij de laadplaats gaan en voor een visueel bewijs zorgt om exact te kunnen controleren wat verzonden is. In geval van een klacht van een klant, kunnen we het fotobewijs gebruiken en leggen we een zeer nuttige audit trail aan met onze groeiende bibliotheek met verzendgegevens", aldus Henrik Rosendahl Laursen.
Visibiliteit van de werkzaamheden
Het systeem is geïntegreerd met de WMS-oplossing van Danfoss, zodat het management op elk moment een duidelijk beeld heeft van de laadplaatswerkzaamheden en fouten heel snel opgemerkt en gecorrigeerd kunnen worden.
Nul fouten
Het systeem kan pallets scannen tot op een hoogte van 2 meter. "In de 10 maanden sinds we het in gebruik genomen hebben, is er geen enkele verzendfout meer voorgekomen. Het systeem waarschuwt ons namelijk als een chauffeur de verkeerde pallets in zijn truck wil laden. De kwaliteit is jaar na jaar beduidend verbeterd."
ROI binnen 12 maanden
Bij de oorspronkelijke projectdefinitie hoopte Danfoss op een return on investment (ROI) binnen 2 jaar. Dankzij de indrukwekkende eerste resultaten kon deze prognose bijgesteld worden naar 12 maanden. "We kunnen vergissingen en laadfouten veel beter traceren dan we oorspronkelijk gedacht hadden. Er kwamen namelijk ook fouten naar voren op andere plaatsen dan de laadplaats en die werken we nu ook weg", vertelt Henrik Rosendahl Laursen. "Zo waren er bijvoorbeeld systeemfouten waardoor een verkeerde bestemming opgegeven werd met als gevolg dat een doos op de verkeerde pallet werd geplaatst."
Beter naleven van de planning
De planning wordt ook beter nageleefd en Danfoss kan de zendingen nu veel preciezer plannen en afstemmen op de wensen van de klant. Als in het verleden een klant goederen bestelde voor levering op een specifieke dag, dan was er geen overzicht van de speciale orderwensen of een mechanisme om te controleren of de goederen niet te vroeg verzonden werden. Als de items op voorraad waren, werden de orders naar de laadplaats gebracht zonder informatie en de operatoren verzonden deze dan zo snel mogelijk, ongeacht de gevraagde leveringsmomenten. "Als een pallet nu te vroeg geladen wordt voor verzending, dan wordt een foutmelding gegeven en wordt het proces stopgezet. Zo kunnen we ervoor zorgen dat de goederen helemaal overeenkomstig de wensen van de klant verzonden worden, wat erg belangrijk is voor de klantentevredenheid."
Tegelijk laden van trucks
Niet alleen is een einde gemaakt aan de fouten, maar ook de efficiëntie is verbeterd. De laadtijden zijn weliswaar hetzelfde als voorheen, maar de operatoren kunnen nu meerdere trucks tegelijk laden zonder fouten te maken. Dit heeft als bijkomend voordeel dat Danfoss het magazijnpersoneel flexibeler in kan zetten en hen van dag tot dag in kan delen daar waar de prioriteiten liggen. Behalve dat dit bijdraagt aan de productiviteit in het magazijn, betekent dit ook dat het werk van de operatoren meer afwisselend is en dat ze meer inzicht krijgen in het reilen en zeilen van het magazijn.
"Elke keer dat we een fout onderscheppen betekent dit dat de klant op het juiste moment de juiste goederen zal ontvangen, wat ten goede komt aan de klantentevredenheid. Voorheen kwamen we pas achter fouten als onze expediteur afwijkingen rapporteerde, maar nu kunnen we deze zelf achterhalen tijdens het laadcontroleproces. We krijgen geweldige reacties van de expediteurs omdat ze met de foto's die gemaakt worden van elke zending veel gemakkelijker de goederen kunnen vinden in elke lading", zegt Henrik Rosendahl Laursen.
Sinds de implementatie van de laadcontrole-oplossing ZetesMedea heeft Danfoss zijn geautomatiseerde manier van werken gedemonstreerd aan andere bedrijven en zeer positieve reacties gekregen. "Onze branchegenoten zijn erg onder de indruk van wat we kunnen en de snelheid waarmee we tegenwoordig 100% nauwkeurige orders verwerken voor verzending, nu er geen fouten meer voorkomen bij het laadpunt", vervolgt Henrik Rosendahl Laursen. "Ik denk dat veel bedrijven baat kunnen hebben bij de oplossing en zelf zijn we ook aan het kijken hoe we het gebruik ervan kunnen uitbreiden naar andere magazijnen en het proces verder kunnen verbeteren door ons papierwerk te vereenvoudigen."
Sinds we het in gebruik genomen hebben, is er geen enkele verzendfout meer voorgekomen. Het systeem waarschuwt ons namelijk als een chauffeur de verkeerde pallets in zijn truck wil gaan laden. Henrik Rosendahl Laursen, Warehouse & Distribution Consultant, Danfoss