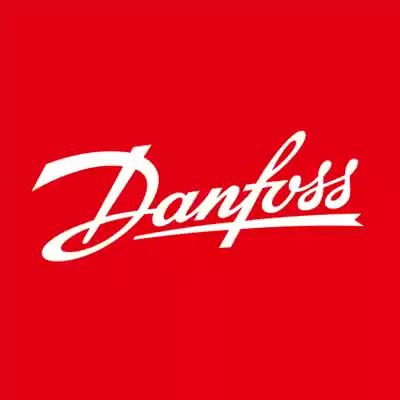
Con sede en Nordborg (Dinamarca), Danfoss es una empresa líder mundial en el desarrollo y la producción de soluciones energéticas eficientes, con una plantilla de 23 000 trabajadores y 61 fábricas. Sus clientes, que van desde usuarios particulares y propietarios de fábricas hasta constructores y socios industriales, están repartidos por más de 100 países. En el almacén principal de Danfoss, situado en Roedekro, cada año se registran 1,5 millones de pedidos y 80 000 entregas. Cada día circulan por este almacén unos 100 camiones, que realizan más de 350 repartos diarios a distribuidores situados en diferentes áreas geográficas.
Objetivo:
- Mejorar la exactitud de la carga
- Eliminar los errores de envío
- Reducir los plazos de entrega
- Reducir los costes logísticos
Solución:
- Verificación de carga de ZetesMedea
- Tecnología de visión ImageID
- Banco de imágenes para el control visual en tiempo real
Resultado:
- Rentabilización de la inversión en 12 meses
- Comprobantes visuales de carga y de estado
- Mayor satisfacción de los clientes gracias a la reducción de los errores de envío
Coste de los errores de verificación de carga
Danfoss sigue unos procedimientos muy estrictos, especialmente al procesar pedidos destinados a países fuera de la Unión Europea. Antes, el proceso de verificación de carga de los vehículos era muy lento, porque era necesario colocar los palés en una zona específica y comprobarlos manualmente antes de cargarlos en los camiones.
Si un palé con destino a un país europeo se colocaba en una ubicación errónea de la zona de carga, se producía un trastorno importante en la operativa. Como los plazos de entrega eran muy ajustados, no se podía dedicar mucho tiempo a verificar si los envíos a países europeos se cargaban en los vehículos correctos. Por ello, con frecuencia se producían errores, que en ocasiones pasaban inadvertidos a Danfoss hasta que se los comunicaba la empresa de transporte.
«Una vez enviamos a Islandia un palé con destino a Italia porque no contábamos con un proceso de verificación eficiente para comprobar que el palé estuviera en el lugar adecuado para cargarse en el camión correcto», se lamenta Henrik Rosendahl Laursen, consultor de almacenes y distribución de Danfoss. Los errores de este tipo causaban verdaderos problemas, porque Danfoss debía asumir el coste de la devolución al almacén y del envío del pedido correcto, que el cliente recibía con retraso.
«No es fácil saber cuántos errores de carga se producían, pero la cifra podría rondar los 600 palés o cajas anuales», afirma Laursen. «En el peor de los casos incluso debíamos enviar los productos por avión para compensar el tiempo perdido porque, aunque la gestión de los costes es importante, todavía lo es más garantizar la satisfacción del cliente».
¿Más personal o automatización?
Debido a la frecuencia de los errores de carga, Danfoss decidió actuar para poner fin a estos problemas y aumentar la productividad. La empresa se planteó si debía ampliar la plantilla del almacén para comprobar de forma manual todos los envíos o adoptar una solución tecnológica que resolviera el problema de la verificación de carga. «Si elegíamos la opción de ampliar la plantilla, lo que más nos preocupaba era si lograríamos aumentar la fiabilidad del proceso de carga teniendo en cuenta los elevados costes laborales», argumenta Laursen. Además, en Danfoss eran conscientes de que si implementaban una solución tecnológica, se beneficiarían de un proceso fiable y uniforme en cada operación, lo que les permitiría establecer un baremo para evaluar los futuros índices de exactitud y productividad.
Tras decidirse por una solución automatizada para mejorar la verificación de carga y la exactitud de los envíos, Danfoss estudió las ofertas de diferentes proveedores y pidió la opinión a otras empresas danesas con operaciones de transporte parecidas. En su análisis observó que la mayoría de las empresas habían optado por una solución personalizada. Sin embargo, Danfoss buscaba una solución estándar que estuviera probada, fuera comercialmente viable y les permitiera actualizarla y mejorarla en el futuro.
Verificación de carga mediante la tecnología de visión
Danfoss concluyó que la solución de verificación de carga de ZetesMedea con tecnología de visión ImageID era la opción más viable y práctica. Esta solución automatizada analiza y detecta las etiquetas automáticamente en cuestión de segundos mediante la tecnología de visión. Integrada en un sistema WMS o ERP y con una cámara de 5 megapíxeles instalada en cada muelle, detecta y lee los códigos de barras de las etiquetas en los palés, las compara con la información de envío y confirma al operario que todo es correcto. También toma imágenes de cada palé, jaula o cajón y las almacena en un banco de imágenes, como garantía de que el pedido se ha cargado y enviado correctamente.
La implementación se inició en el año 2015 con un proyecto piloto en uno de los muelles y, tras realizar los ajustes pertinentes en el proceso, se fue extendiendo a las 14 zonas de carga restantes.
El proyecto se realizó en seis meses, y Danfoss fue marcando los tiempos en función de sus necesidades para definir los requisitos exactos de la solución, adaptar los procesos de envío existentes, crear nuevas etiquetas, acceder a documentación específica en los muelles y aprobar con seguridad cualquier cambio necesario.
Principales ventajas
Comprobantes visuales de carga
«Pronto nos dimos cuenta de que la solución de verificación de carga de ZetesMedea era ideal porque comprobaba los artículos a medida que avanzaban en la zona de carga y proporcionaba un comprobante visual que permitía saber con exactitud qué productos se habían enviado. Si se produce una reclamación de un cliente, podemos recurrir a la prueba fotográfica y contamos con un registro de auditoría que contiene todos nuestros datos de envío», explica Laursen.
Visibilidad de las operaciones
La solución se integra con el sistema WMS de Danfoss, de modo que los responsables del almacén pueden controlar todas las operaciones de carga en cualquier momento y se pueden detectar y corregir los errores en muy poco tiempo.
Cero errores
El sistema puede escanear palés con una altura de hasta dos metros. «En los diez meses que llevamos utilizándolo, no se ha producido ni un solo error de carga, porque el sistema nos avisa si un conductor intenta cargar un palé equivocado en su camión. En conclusión, la mejora en la calidad respecto al año pasado ha sido espectacular».
Rentabilización de la inversión en 12 meses
En la planificación original del proyecto, Danfoss previó que la solución se rentabilizaría en dos años, pero debido a los excepcionales resultados obtenidos esta previsión se ha recortado a la mitad. «Estamos detectando más problemas y errores de carga de los previstos inicialmente porque hemos identificado otras fases del proceso fuera de la zona de carga en las que se producían errores, y estamos trabajando para eliminarlos», añade Laursen. «Por ejemplo, si por error el sistema especificaba un destino equivocado en una caja, esta se colocaba en un palé incorrecto».
Planificaciones más exactas
La exactitud de las planificaciones también ha mejorado, y ahora en Danfoss los envíos se realizan atendiendo a las necesidades exactas de los clientes. Antes, si un cliente realizaba un pedido para un determinado día, no había forma de gestionar este tipo de peticiones especiales ni se controlaba si las mercancías se enviaban demasiado pronto. Los pedidos se enviaban a la zona de carga sin información y los operarios cargaban los camiones con la máxima rapidez —siempre y cuando hubiese existencias—, sin tener en cuenta las peticiones de los clientes. «Ahora cuando los palés se cargan demasiado pronto, se genera un mensaje de error y el proceso se detiene. De este modo, los pedidos enviados cumplen con los requisitos de los clientes y esto aumenta considerablemente su nivel de satisfacción».
Carga simultánea de camiones
Además de eliminar los errores de carga, también se ha mejorado la eficiencia. Aunque el tiempo de carga es el mismo, los operarios ahora pueden trabajar en más camiones de forma simultánea sin cometer errores. Esto permite a Danfoss organizar al personal del almacén de una forma más flexible y reasignarlo en función de las prioridades diarias. Aparte de armonizar la productividad, los empleados pueden trabajar en diferentes tareas y ser más conscientes de las operaciones que se realizan en el almacén.
«Cada vez que detectamos un error, logramos que el cliente reciba el pedido correcto en el momento oportuno, y eso se traduce en una mayor satisfacción por su parte. Antes nuestros transportistas nos comunicaban los errores posteriormente mediante un informe de discrepancias, pero ahora los detectamos nosotros mismos durante el proceso de verificación de carga. Además, gracias a las imágenes de cada envío, los transportistas localizan las mercancías más fácilmente», afirma Laursen.
Desde su implantación, Danfoss ha mostrado la solución de verificación de carga de ZetesMedea a otras empresas y ha recibido comentarios muy positivos. «Otras empresas del sector han quedado gratamente sorprendidas con nuestra forma de trabajar y con la velocidad a la que ahora procesamos los pedidos, eliminando los errores en la zona de carga», asevera Laursen. «Estoy convencido de que muchas empresas se podrían beneficiar de esta solución; también estamos buscando la forma de implantarla en el resto de nuestros almacenes y de optimizar todavía más el proceso simplificando el papeleo».
«En estos diez meses no se ha producido ni un solo error de carga, porque el sistema nos avisa si un conductor carga un palé equivocado en su camión». Henrik Rosendahl Laursen, consultor de almacenes y distribución de Danfoss.