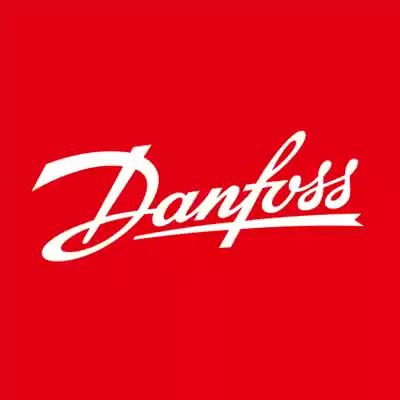
Basé à Nordborg au Danemark, Danfoss est un leader mondial dans le développement et la production de solutions écoénergétiques. L'entreprise compte plus de 23 000 employés, 61 usines et de nombreux clients (des particuliers aux propriétaires d'installations industrielles, en passant par des promoteurs immobiliers et des partenaires industriels) dans plus de 100 pays. L'entrepôt principal de Danfoss, situé à Roedekro, traite 1 million et demi de lignes de commande et quelque 80 000 livraisons par an. Chaque jour, près de 100 camions arrivent et repartent, soit plus de 350 commandes clients exécutées et expédiées à des partenaires de distribution dans de nombreux endroits.
Objectif :
- Améliorer la précision de chargement
- Supprimer les erreurs d'expédition
- Réduire les délais d'exécution des livraisons et les coûts logistiques
Solution :
- Solution de vérification de chargement ZetesMedea
- Technologie de vision industrielle ImageID
- Piste d'audit en temps réel avec une banque d'images (ImageBank)
Résultat :
- ROI complet en 12 mois
- Preuve visuelle du chargement et de son état
Satisfaction client accrue
Vérification de chargement : le coût de l'inefficacité
Danfoss respecte des procédures de conformité rigoureuses, en particulier en ce qui concerne les expéditions hors Union européenne. L'ancien processus de vérification de chargement prenait beaucoup de temps : les palettes étaient placées dans une zone de sortie et les documents papier contrôlés manuellement avant que les marchandises soient chargées et expédiées.
Si une palette destinée à un pays européen était placée au mauvais endroit dans la zone de chargement, cela perturbait considérablement les opérations. En outre, en raison des délais très serrés, Danfoss ne disposait que d'un court laps de temps pour vérifier que les expéditions à destination de l'UE étaient chargées dans les bons camions. Ainsi, des erreurs humaines se produisaient fréquemment, et celles-ci n'étaient parfois identifiées que plus tard, lorsque les transitaires informaient Danfoss que les marchandises reçues pour expédition étaient incorrectes.
« Il nous est arrivé d'expédier vers l'Islande une palette destinée à l'Italie pour la simple raison que nous ne disposions pas d'un processus de contrôle de chargement robuste pour vérifier que la bonne palette se trouvait au bon endroit pour être chargée dans le bon camion », se souvient Henrik Rosendahl Laursen, Consultant en entreposage et distribution chez Danfoss. De telles erreurs entraînaient des perturbations et des désagréments importants, dans la mesure où il fallait retourner les marchandises vers l'entrepôt aux frais de Danfoss, puis réexpédier la commande correcte, ce qui engendrait parfois des retards de livraison pour le client.
« Il est difficile de quantifier la fréquence des erreurs de chargement, mais on peut raisonnablement estimer leur nombre à quelque 600 palettes/cartons par an », déclare Henrik Rosendahl Laursen. « Dans les pires cas, nous devions expédier les marchandises correctes par avion pour rattraper le temps perdu et garantir la satisfaction du client, quitte à ne plus maîtriser nos coûts. »
Renfort de main-d'œuvre ou automatisation ?
Ces problèmes ont décidé Danfoss à améliorer l'exactitude du chargement des véhicules pour atteindre le double objectif d'éliminer les erreurs d'expédition et de booster la productivité. La société a dès lors évalué s'il fallait recruter du personnel supplémentaire en entrepôt pour procéder à la vérification physique de tous les colis ou adopter une solution technologique à même de corriger les problèmes de vérification de chargement. « Dans le scénario d'un renfort de main-d'œuvre, notre plus grande préoccupation était que la fiabilité soit à la hauteur du coût salarial élevé », explique Henrik Rosendahl Laursen. Par ailleurs, l'entreprise a compris que la mise en œuvre d'une solution technologique garantirait à chaque fois un processus et un rendement fiables et stables — un avantage indéniable pour évaluer les niveaux de précision et de productivité à l'avenir.
Une fois la décision prise d'opter pour une solution automatisée, Danfoss a examiné plusieurs éditeurs de solutions et demandé l'avis de nombreux fournisseurs de services de transport similaires au Danemark. L'entreprise a ainsi constaté que la majorité des entreprises avait préféré une approche personnalisée. Toutefois, Danfoss tenait à acquérir une solution éprouvée, standardisée et commercialement viable qui lui permettrait de tirer parti de mises à jour et d'améliorations technologiques.
Vérification de chargement par vision industrielle
Danfoss est arrivé à la conclusion que la solution de vérification de chargement ZetesMedea, optimisée par la technologie de vision industrielle ImageID, était l'option la plus viable et la plus pratique. Cette solution automatisée s'appuie sur une fonction de capture de données par vision industrielle pour détecter et analyser automatiquement les étiquettes des palettes en quelques secondes. Grâce à l'intégration avec un système WMS ou ERP et à un appareil photo 5 mégapixels installé dans chaque zone de chargement, la solution détecte et lit instantanément le code à barres des étiquettes, valide ces données par rapport aux informations d'expédition et signale à l'opérateur s'il peut ou non charger les marchandises. Elle capture également l'image de chaque caisse, palette ou chariot et l'enregistre dans une banque d'images dédiée pour apporter la preuve irréfutable qu'une commande a été correctement chargée et expédiée.
La mise en œuvre a débuté en 2015 par un projet pilote dans une seule zone de chargement et a été élargie, après quelques ajustements, à l'ensemble des 14 aires de chargement.
Le projet s'est achevé au bout de 6 mois — un délai justifié par divers besoins exprimés par Danfoss, à savoir définir des exigences précises par rapport à la solution, réaligner les processus d'expédition existants, produire de nouvelles étiquettes, accéder à des documents spécifiques dans la zone de chargement ou encore être en mesure d'approuver avec certitude toute modification.
Principaux avantages
La preuve en image
« La solution de vérification de chargement ZetesMedea s'est rapidement imposée comme l'approche idéale, notamment parce qu'elle contrôle automatiquement les marchandises qui se déplacent dans l'aire de chargement et fournit une preuve visuelle de l'expédition. Ces clichés sont très utiles en cas de réclamation de la part d'un client, et ils nous permettent en outre de mettre en place une piste d'audit très pratique pour notre bibliothèque de données d'expédition en croissance constante », se réjouit Henrik Rosendahl Laursen.
Visibilité sur les opérations
Dans la mesure où le système est intégré avec la solution WMS de Danfoss, la direction dispose d'une visibilité permanente sur les opérations dans les zones de chargement et la moindre erreur peut être très rapidement identifiée et corrigée.
Zéro erreur
Le système lit les codes à barres de palettes pouvant atteindre 2 mètres de haut. « En 10 mois d'utilisation, nous n'avons rencontré aucune erreur de chargement parce que le système nous avertit dès qu'un chauffeur ne charge pas les bonnes palettes dans le bon camion. Globalement, la qualité s'est considérablement améliorée par rapport à l'an passé. »
Retour sur investissement en 12 mois
Lors de la qualification initiale du projet, Danfoss avait misé sur un retour sur investissement complet après deux ans, mais ces prévisions ont été ramenées à 12 mois au vu des premiers résultats exceptionnels. « Nous repérons davantage d'imprécisions et d'erreurs de chargement que ce qui était initialement prévu, parce que nous avons identifié d'autres étapes dans le processus, en dehors de la zone de chargement, au cours desquelles des erreurs se produisent et que nous veillons à supprimer également », ajoute Henrik Rosendahl Laursen. « Par exemple, si une destination incorrecte était mentionnée suite à une erreur système, les cartons étaient placés sur les mauvaises palettes. »
Ordonnancement plus précis
L'ordonnancement étant plus précis, Danfoss est en mesure de mieux gérer les calendriers d'expédition pour répondre aux besoins des clients. Auparavant, lorsqu'un client commandait des marchandises à livrer un jour précis, l'entreprise n'avait aucune visibilité sur les demandes de commande spéciale et n'était pas à même de contrôler si les marchandises étaient expédiées trop tôt. Les commandes parvenaient dans l'aire de chargement sans aucune information, et les opérateurs tâchaient de les expédier aussi vite que possible (à condition que les articles soient disponibles en stock), quel que soit le délai demandé par le client. « Désormais, si une palette est chargée pour expédition trop tôt, le système génère un message d'erreur et le processus est interrompu. Ainsi, nous sommes certains que l'expédition des marchandises est parfaitement conforme aux attentes des clients, ce qui améliore grandement leur niveau de satisfaction. »
Chargement simultané de camions
Le processus de chargement est exempt d'erreurs, mais aussi plus efficace. En effet, si les temps de chargement sont restés identiques, les opérateurs peuvent désormais prendre en charge plusieurs camions simultanément sans commettre d'erreurs. Autre avantage pour Danfoss : l'entreprise peut utiliser le personnel d'entrepôt de manière plus flexible et le redéployer selon les priorités quotidiennes. Ainsi, les niveaux de débits sont optimisés et les employés, qui exercent diverses fonctions, acquièrent une meilleure compréhension des opérations en entrepôt.
« Chaque erreur repérée signifie que le client va recevoir les bonnes marchandises au bon moment, pour un degré de satisfaction supérieur. Par le passé, nous n'étions avertis d'une erreur que lorsque les transitaires nous envoyaient un rapport d'anomalies. Aujourd'hui, nous détectons nous-mêmes les erreurs lors du processus de contrôle de chargement. Nos transitaires sont ravis, notamment parce que les clichés capturés par le système leur permettent de retrouver plus facilement les marchandises pour chaque expédition », poursuit Henrik Rosendahl Laursen.
Depuis la mise en œuvre de la solution de vérification de chargement ZetesMedea, Danfoss a eu l'occasion de présenter son approche automatisée à d'autres entreprises et a reçu un retour très positif. « Nos homologues dans le secteur sont très impressionnés par nos capacités et par la vitesse à laquelle les commandes sont exécutées en vue de l'expédition avec une extrême précision, rendue possible par l'absence d'erreurs au point de chargement », conclut Henrik Rosendahl Laursen. « Il me semble que de nombreuses entreprises pourraient tirer parti de cette solution. Par ailleurs, nous réfléchissons déjà à la manière de l'étendre à nos autres entrepôts et envisageons d'améliorer encore le processus en simplifiant et en facilitant les formalités administratives. »
« En 10 mois d'utilisation, nous avons pu éviter toute erreur de chargement.» Henrik Rosendahl Laursen, Consultant en entreposage et distribution, Danfoss