Om concurrentievoordeel te behouden hebben logistieke dienstverleners en retailers het verzamelen van alle orders in hun magazijnen geautomatiseerd met pick-to-cart, pick-to-light, voice-picking en andere systemen. Met als resultaat aanzienlijke efficiencyverbeteringen. Ondanks het succes van die ICT-oplossingen, is er vaak nog meer efficiencywinst te behalen door logistieke processen anders te organiseren. Een voorbeeld daarvan is de 38% verbetering die A.S. Watson heeft gerealiseerd met multi-order-picking.
Jeffrey Verberne, manager business consultancy bij Zetes, beschrijft hoe bedrijven een multi-order picking oplossing kunnen implementeren en hoe daarbij bottlenecks te voorkomen zijn.
1. Identificeer de optimale orderverzamelmethode
De optimale methode voor het verzamelen van orders is afhankelijk van veel invloedsfactoren, zoals het assortiment en omloopsnelheid daarvan, de magazijn- omvang, het aantal klantorders en orderregels, gewenste levertijden etc., Zonder een analyse daarvan en inventarisatie van de belangrijkste logistieke knelpunten levert elke investering in een automatiseringsoplossing niet het optimale rendement op.
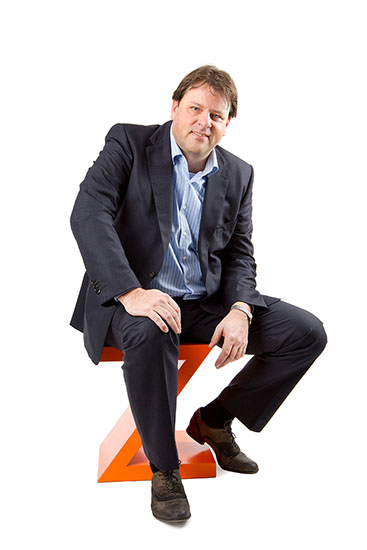
Verder is het belangrijk te berekenen welke methode van orderpicken en bijbehorende techniek de meeste voordelen oplevert. Enkelvoudig of meervoudig (single- of multi-order-picking) en pick-to-cart, pick-to-light, voicepicking of varianten daarvan.
2. Maak onderscheid tussen dynamisch of statisch order-picking
Om de beste methode voor het verzamelen van orders te vinden, is het belangrijk onderscheid te maken tussen dynamisch en statisch orderpicken.
Dynamic order picking
Bij dynamisch orderpicken blijven de orderpickers op een vaste positie staan en worden alle bestelde artikelen binnen hun handbereik aangeboden. Bijvoorbeeld via een gerobotiseerde Autostore. Een belangrijk voordeel van deze methode is het elimineren van alle loop- of rijafstanden.
Static order picking
Bij statisch orderpicken bezoekt elke orderpicker de opslaglocaties van alle bestelde goederen, lopend of met een pickcar of heftruck.
Verder is bij het statisch orderverzamelen nog onderscheid te maken tussen single- en multi-order-picking. Als de meeste orders een groot aantal orderregels bevat, zijn de loop- of rijtijden tussen alle benodigde artikelen vaak klein en is enkelvoudig picken waarschijnlijk de beste oplossing. Als echter elke order een klein aantal bestelde artikelen bevat, zoals onder andere voorkomt bij webwinkels voor consumenten, kan multi-order-picking aanzienlijke tijdwinst opleveren. Verder kan het voor klanten nodig zijn meerdere orders te picken binnen een bepaalde tijdsperiode, of voor een bepaalde vervoerder, wat wave-picking wordt genoemd. Tenslotte zijn grote distributiecentra te verdelen in zones, waarin het personeel dan op basis van zone-picking orderregels verzamelen.
3. Analyseren en minimaliseren rij- en loopafstanden
De keuze voor single- of multi-order-picking kan tot aanzienlijke efficiencyverschillen leiden. Bij multi-order-picking is meestal het primaire doel de rij- en loopafstanden van alle orderpickers te minimaliseren. Door in één route de producten voor meerdere orders te laten picken (multi-order), of de totale hoeveelheid van bepaalde artikelen voor meerdere klanten te verzamelen (artikelgericht samenvoegen).
Bij beide varianten moeten alle gepickte producten ook nog op een slimme manier worden toegekend aan de juiste klantorders. Bij voorkeur al tijdens het orderpicken, via het gebruik van controlegetallen of kleurcodes en rolcontainers of verzenddozen per order. Als die uitsplitsing na het picken namelijk veel tijd kost, of tot fouten leidt, daalt de mogelijke efficiencyverbetering of leverbetrouwbaarheid. Uiteraard is de extra te behalen efficiencyverbetering met multi-order-picking net als bij andere methoden afhankelijk van het assortiment, het aantal orderregels per order, het aantal orderpickers en de magazijngrootte, dus altijd maatwerk."
4. Procesanalyse en businesslogica
Voor het inzichtelijk maken van de voordelen en besparingen die met multi-order-picking te realiseren zijn, is altijd een analyse van de administratieve orderverwerking en het orderpicken nodig.
De belangrijkste vragen daarbij zijn:
• Wat zijn momenteel de rij- en loopafstanden van alle orderpickers en hoeveel colli verzamelen zij gemiddeld per uur?
• Leent het assortiment of een deel daarvan zich voor artikel- of ordergericht multi-order- picking en past dit binnen de tijdzones waarin de orders gepickt mogen worden?
Voor veel kleine webwinkelorders van particulieren is het vaak niet zinvol multi-order-picking te implementeren, vanwege de verwachte leversnelheid (o.a. ‘same day delivery). Logistiek dienstverleners en retailers met grote magazijnen en tientallen orderpickers hebben echter dusdanige orderstromen dat een investering in multi-order-picken wellicht al in korte tijd is terug te verdienen. Uiteraard is het daarbij tevens van belang of het combineren van orders al wordt ondersteund door het aanwezige ERP- en/of WCS/WMS-systeem. Anders is die integratie met aanvullende businesslogica voor het maken van volumetrische berekeningen en aanpassingen van een voicedialoog toe te voegen.
Hoe werkt dit in de praktijk bij A.S. Watson?
A.S. Watson, het concern achter Kruidvat, Trekpleister, ICI PARIS XL, Pour Vous en Prijsmepper en daarmee marktleider in Health & Beauty, is een goed voorbeeld van hoe bedrijven de efficiency tot wel 38% kunnen verbeteren met multi-order-picken.
Coen Mulder – Functioneel Control Supply Chain Development bij A.S. Watson, licht toe "In ons magazijn hier in Heteren werken wij al een aantal jaren met voice-picking, gebaseerd op de ZetesMedea-oplossing. Onze orderverwerking is opgesplitst in drie stromen, te weten alle producten uit het gangbare assortiment, actieproducten en e-fulfilment bestellingen.
"Na een periode enkelvoudige orders te hebben verzameld, waarbij alle orderpickers het volledige magazijn doorrijden, zijn wij samen met Zetes gaan kijken naar de mogelijkheden om onze rijafstanden te minimaliseren. Daarbij kwamen wij tot de conclusie dat het combineren van orders ondersteund door volumeberekeningen voor het meenemen van de beste orderdragers (pallets of bakken), zo'n 16% efficiëncyverbetering kon opleveren. Op basis van die businesscase hebben wij vervolgens samen multi-order-picking geïmplementeerd".
Jaqueline van Oostrum, Supply Chain and Logistics Project manager bij A.S. Watson, vertelt hoe de 38% efficiencyverbetering is bereikt: "Wij hebben behalve de al genoemde volumeberekeningen voor onze orderdragers en een uitbreiding van de voice-dialoog voor batchpicking ook een aantal palletwagens aangepast. Uiteindelijk bepaalt de combinatie van software- en materieelaanpassingen en betrokkenheid van alle medewerkers namelijk de maximaal te behalen verbetering.
“Terugkijkend op dit project heeft onze implementatie van multi-order-picking voor het gangbare assortiment ieders verwachting overschreden met een efficiëncyverhoging van maar liefst 38%”- Jaqueline van Oostrum, Supply Chain and Logistics Project manager bij A.S. Watson.
Behalve het minimaliseren van de rijafstanden levert multi-order-picken nog extra tijdbesparingen op. Bijvoorbeeld doordat medewerkers elkaar niet meer hinderen, of hoeven te wachten in de magazijngangen. Terugkijkend op dit project heeft onze implementatie van multi-order-picking voor het gangbare assortiment ieders verwachting overschreden met een efficiëncyverhoging van maar liefst 38%. Het gemiddeld aantal colli dat bij deze orderstroom per uur wordt verzameld is sindsdien toegenomen van 90 naar 125.