Per avvantaggiarsi sulla concorrenza, fornitori di servizi logistici e retailer hanno dotato i propri magazzini di sistemi di picking automatizzato degli ordini, implementando tecnologie di pick-to-cart, pick-to-light, picking vocale ed altre ancora. Tuttavia, nonostante il successo di queste soluzioni ICT, è possibile aumentare notevolmente l'efficienza anche riorganizzando processi logistici chiave.
Jeffrey Verberne, Logistics Business Consultant presso Zetes, getta uno sguardo su come le aziende possono implementare una soluzione di picking multi-ordine, evitando ogni potenziale ostacolo.
1. Identificazione del metodo ottimale di picking degli ordini
Il metodo ottimale di picking degli ordini dipende da molti fattori, quali la gamma di prodotti, i volumi nei periodi di punta, le risorse, le dimensioni del magazzino, il numero di ordini da gestire e i tempi di consegna desiderati. Senza un'analisi di questi fattori e l'identificazione dei principali colli di bottiglia della logistica, qualsiasi investimento in soluzioni di automazione non produrrà una soluzione ottimale.
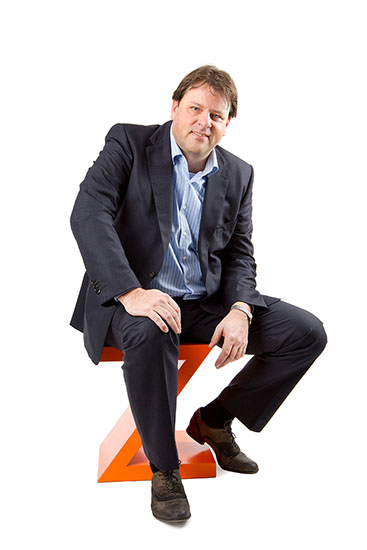
È anche importante determinare quale metodo di picking degli ordini e quale tecnologia sottostante offriranno i maggiori vantaggi: picking di ordini singoli o di più ordini contemporaneamente, pick-to-cart, pick-to-light, picking vocale o altra opzione.
2. Distinzione tra picking dinamico o statico
Per trovare il miglior metodo di picking degli ordini, è importante distinguere tra il picking dinamico e quello statico. Vediamo di chiarire questo gergo tecnico:
Picking dinamico degli ordini
Gli operatori restano in una posizione fissa e tutti i prodotti ordinati sono disponibili entro la loro portata - ad esempio, in un magazzino robotizzato. Il picking dinamico degli ordini offre l'importante vantaggio di eliminare le distanze di viaggio.
Picking statico degli ordini
Ogni operatore si reca nei vari punti di stoccaggio dei prodotti ordinati, a piedi o con un carrello di raccolta o un fork lift.
Altra importante differenza rispetto al picking statico è la possibilità di scegliere tra picking di singoli ordini o multi-ordine. Se la maggior parte degli ordini è composta da un numero elevato di SKU (Stock Keeping Unit), i tempi di trasporto tra i prodotti sono spesso brevi, quindi la migliore soluzione sarà probabilmente il picking di singoli ordini. Tuttavia, se è presente solo un piccolo numero di prodotti per ciascun ordine, il picking multi-ordine può fornire risultati migliori, consentendo di risparmiare tempo. Può anche essere necessario selezionare più ordini entro una finestra di tempo predefinita per clienti o vettori specifici, un metodo chiamato "wave picking". Infine, in grandi centri di distribuzione, lo staff può essere assegnato a zone in cui vengono preparati gli ordini in base agli SKU specifici di una certa area.
3. Valutazione e riduzione delle distanze di viaggio
La scelta tra picking di singoli ordini o di più ordini può portare a notevoli differenze di efficienza. L'obiettivo primario del picking multi-ordine è ridurre al minimo le distanze di viaggio per gli operatori. Ciò si ottiene ad esempio selezionando tutti i prodotti di più ordini (picking multi-ordine) su un singolo percorso o selezionando contemporaneamente la quantità totale di uno SKU specifico per più clienti (batch picking).
Con queste due opzioni, tutti i prodotti prelevati devono anche essere assegnati agli ordini dei clienti corretti in modo intelligente. Questa operazione viene preferibilmente effettuata durante il picking, utilizzando numeri di controllo o codici colore e roller container o scatole per spedizione separate per ciascun ordine. Se la suddivisione dei prodotti dopo il picking richiede troppo tempo o è causa di errori, il potenziale miglioramento dell'efficienza si riduce e con esso anche l'affidabilità delle consegne. L'aumento dell'efficienza che può essere ottenuto con il picking multi-ordine dipende dalla gamma di prodotti, dal numero di SKU per ordine, dal numero di operatori e dalle dimensioni del magazzino: pertanto, come per gli altri metodi, il suo uso deve sempre essere considerato caso per caso.
4. Analisi dei processi e logica aziendale
Per sapere se il picking multi-ordine offre vantaggi e possibilità di risparmio, è necessario analizzare i processi di gestione e di picking degli ordini.
Ponendosi le seguenti domande:
• Quali sono le attuali distanze di spostamento di tutti gli operatori che effettuano il picking degli ordini e quanti pacchi all'ora preparano in media?
• La gamma di prodotti o una parte dei prodotti è idonea al picking di singoli ordini o multi-ordine e si adatta ai tempi disponibili per il picking?
In caso di tanti piccoli ordini singoli, spesso non vale la pena implementare il picking multi-ordine, a causa dei tempi di consegna previsti, ad esempio consegna in giornata. Tuttavia, le quantità di ordini gestiti da fornitori di servizi logistici e retailer, con magazzini di grandi dimensioni e decine di operatori, possono essere tali da giustificare un investimento nel picking multi-ordine e da offrire ROI brevi. Altra importante considerazione da non sottovalutare è la capacità dei sistemi ERP e/o WCS/WMS esistenti di supportare il picking multi-ordine. Se i sistemi preesistenti non dispongono di tale capacità, sarà necessario introdurre anche un ulteriore strato di business logic per il calcolo delle quantità e per la calibrazione dei comandi vocali.
Come funziona in pratica?
A.S. Watson, società che detiene i marchi Kruidvat, Trekpleister, ICI PARIS XL, Pour Vous e Prijsmepper ed è pertanto leader di mercato in Olanda nel settore salute e bellezza, rappresenta un grande esempio di come le aziende possano trarre vantaggio da un aumento dell'efficienza del 38% implementando il picking multi-ordine.
Coen Mulder, Functional Control Supply Chain Development di A.S. Watson, spiega: "Per diversi anni, nel nostro magazzino qui a Heteren abbiamo usato il picking vocale , basato sulla soluzione ZetesMedea. La gestione degli ordini è suddivisa in tre flussi: tutti i prodotti dell'assortimento corrente, i prodotti con offerte speciali e gli ordini elettronici".
"Dopo aver utilizzato il picking di ordini singoli per un certo periodo, con tutti gli operatori che si spostavano per l'intero magazzino, abbiamo cercato con Zetes modi per ridurre al minimo le distanze percorse. Siamo giunti alla conclusione di poter ottenere circa il 16% di miglioramento dell'efficienza combinando gli ordini con il calcolo delle quantità, per permettere agli operatori di portare con sé il supporto più adatto per il trasporto dei prodotti degli ordini (pallet o contenitori). Sulla base di questo business case, abbiamo quindi implementato congiuntamente il picking multi-ordine".
Parlando dell'incremento di efficienza del 38%, Jaqueline van Oostrum, Supply Chain and Logistics Project Manager presso A.S. Watson, aggiunge: "Oltre ai calcoli della quantità precedentemente indicati, per i nostri operatori e all'ampliamento dell'interazione vocale con il sistema per il batch picking, abbiamo aggiunto anche un certo numero di transpallet. In definitiva, ciò che assicura il massimo miglioramento possibile è la combinazione di modifiche al software e alle apparecchiature, oltre all'impegno di tutti i dipendenti".
Constatiamo che il risultato dell'implementazione del picking multi-ordine per l'assortimento attuale ha superato le aspettative, assicurando un impressionante miglioramento dell'efficienza pari al 38%. Jaqueline van Oostrum, Supply Chain and Logistics Project Manager
"Assieme alla riduzione delle tratte percorse dagli operatori, il picking multi-ordine consente di ottenere ulteriori risparmi di tempo, ad esempio perché gli operatori non si ostacolino a vicenda o non debbano attendere nelle corsie del magazzino. Esaminando il progetto a posteriori, constatiamo che il risultato dell'implementazione del picking multi-ordine per l'assortimento attuale ha superato le aspettative, assicurando un impressionante miglioramento dell'efficienza pari al 38%. Il numero medio di pacchi/ora preparati con questo metodo di picking è aumentato da 90 a 125".