Um wettbewerbsfähig zu bleiben, haben Logistikdienstleister und Handelshäuser auf die automatische Auftragskommissionierung in ihren Lagern umgestellt: mit Pick-to-Cart, Pick-to-Light, Voice-Kommissionierung und weiteren Technologien. Der Erfolg dieser IKT (Informations und Kommunikationstechnik)-Lösungen ist unbestritten. Erheblich höhere Effizienzgewinne lassen sich mit der Umstrukturierung der wichtigsten Logistikprozesse erzielen.
Jeffrey Verberne, Logistics Business Consultant bei Zetes, beschreibt, wie Unternehmen eine Multi-Order Picking-Lösung implementieren können und wie sich potenzielle Hindernisse dabei vermeiden lassen.
1. Die optimale Methode für die Auftragskommissionierung identifizieren
Welche Methode für die Auftragskommissionierung optimal ist, hängt von zahlreichen Faktoren ab: Produktsortiment, Mengen in Spitzenzeiten, Ressourcen, Größe des Lagers, Anzahl der Kundenaufträge und gewünschten Lieferzeiten. Ohne Analyse dieser Faktoren und Identifizierung von entscheidenden Engpässen in der Logistik, wird jede Investition in eine automatisierte Lösung keine optimale Effizienz erzielen.
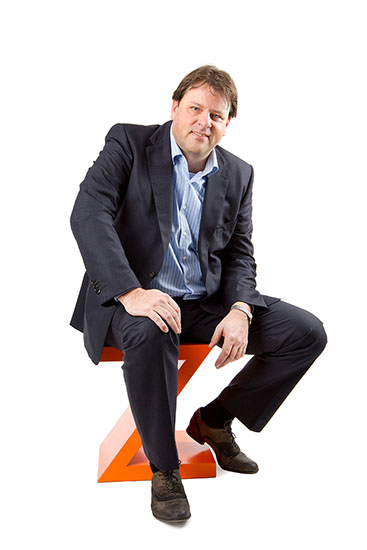
Wichtig ist auch die Entscheidung, welche Methode für die Auftragskommissionierung und welche zugrunde liegende Technologie die meisten Vorteile bringt: ob jeder Auftrag einzeln kommissioniert werden soll oder mehrere Aufträge zusammen, Pick-to-Cart, Pick-to-Light, Pick-by-Voice oder eine andere Möglichkeit.
2. Zwischen statischer und dynamischer Auftragskommissionierung unterscheiden
Um die optimale Methode für die Auftragskommissionierung zu ermitteln, muss zwischen dynamischer und statischer Auftragskommissionierung unterschieden werden. Das bedeutet:
Dynamische Auftragskommissionierung
Die Anwender haben eine feste Position, und alle bestellten Artikel werden ihnen in Reichweite bereitgestellt – beispielsweise in einem robotisierten Lager. Die dynamische Auftragskommissionierung bietet einen wichtigen Vorteil: Alle Wege entfallen.
Statische Auftragskommissionierung
Jeder Mitarbeiter in der Kommissionierung geht für alle bestellten Artikel zum jeweiligen Lagerstandort. Die Wege werden entweder zu Fuß oder mit einem Kommissionierwagen oder Gabelstapler zurückgelegt.
Innerhalb der statischen Auftragskommissionierung wird noch zwischen Single-Order Picking und Multi-Order Picking unterschieden. Wenn die meisten Aufträge eine hohe Anzahl von SKUs (Stock Keeping Units) aufweisen, sind die Wegzeiten zwischen den Artikeln oft kurz. Single-Order Picking ist hierfür vermutlich die beste Lösung. Enthält jede Bestellung hingegen nur eine kleine Anzahl von Artikeln, kann das Multi-Order Picking wesentlich zeitsparender sein. Unter Umständen müssen auch mehrere Aufträge innerhalb eines vorgegebenen Zeitfensters für Kunden oder für einen bestimmten Versanddienst zusammengestellt werden. Dies wird als Wave Picking bezeichnet. Schließlich können große Verteilzentren in Zonen aufgeteilt werden, in denen die Mitarbeiter die Auftragskommissionierung aufgrund zonenspezifischer SKUs durchführen.
3. Wege berechnen und minimieren
Je nachdem, ob das Single-Order Picking oder das Multi-Order Picking gewählt wird, kann die Effizienz erheblich variieren. Beim Multi-Order Picking besteht das Hauptziel in der Regel darin, die Wege für alle Kommissionierkräfte zu minimieren. Dazu werden alle Artikel für bestimmte Aufträge auf einer einzigen Strecke kommissioniert (Multi-Order Picking), oder die Gesamtmenge einer bestimmten SKU wird für mehrere Kunden gleichzeitig kommissioniert (Batch Picking).
Bei diesen beiden Möglichkeiten müssen alle kommissionierten Artikel zusätzlich dem richtigen Kunden zugewiesen werden. Das erfordert eine intelligente Methode. Vorzugsweise erfolgt dieser Schritt während der Auftragskommissionierung anhand von Prüfnummern oder Farbkodierungen und einem gesonderten Rollwagen oder Versandkarton für jeden Auftrag. Wenn das Aufteilen der Artikel nach der Kommissionierung zu lange dauert oder zu fehleranfällig ist, geht dies zu Lasten des potenziellen Effizienzgewinns, oder aber die Zuverlässigkeit der Lieferungen wird beeinträchtigt. Wie sehr die Effizienz durch Multi-Order Picking gesteigert werden kann, hängt vom Produktsortiment, der Anzahl der SKUs pro Bestellung, der Anzahl der Kommissionierkräfte und der Größe des Lagers ab (wie andere Methoden auch) und muss daher immer im Einzelfall beurteilt werden.
4. Prozesse und Geschäftslogik analysieren
Um die Vorteile und Einsparungen durch das Multi-Order Picking beurteilen zu können, müssen der Auftragsbearbeitungs- und der Order Picking-Prozess jeweils analysiert werden.
Die folgenden Fragen geben Aufschluss:
• Wie groß sind die derzeitigen Entfernungen, die die Kommissionierkräfte jeweils zurücklegen müssen, und wie viele Packungen pro Stunde kommissionieren sie durchschnittlich?
• Ist das Produktsortiment oder ein Teil des Produktsortiments für das Multi-Order Picking nach Artikeln oder nach Aufträgen geeignet, und passt diese Methode in das Zeitfenster, das jeweils für die Auftragskommissionierung vorgegeben ist?
Bei vielen kleinen Einzelaufträgen lohnt es sich wegen der erwarteten kurzen Lieferfristen (Lieferung oft am selben Tag) oft nicht, das Multi-Order Picking zu implementieren. Die Auftragsströme von Logistikdienstleistern und Handelsunternehmen mit größeren Lagern und Dutzenden Kommissionierkräften sind jedoch groß genug, dass sich eine Investition in das Multi-Order Picking in der Regel innerhalb kurzer Zeit amortisiert. In diesem Zusammenhang muss überlegt werden, ob das bestehende ERP- und/oder WCS-/WMS-System über die nötigen Funktionen zur Unterstützung des Multi-Order Picking verfügt. Wenn die bereits vorhandenen Systeme nicht über die entsprechenden Funktionen verfügen, muss eine zusätzliche Geschäftslogikschicht für die Berechnung der Mengen und Anpassungen an einen Voice-Dialog eingeführt werden.
Wir funktioniert dies in der Praxis?
A.S. Watson, der Konzern hinter Kruidvat, Trekpleister, ICI PARIS XL, Pour Vous und Prijsmepper und somit Marktführer auf dem niederländischen Gesundheits- und Kosmetikmarkt, ist ein sehr gutes Beispiel dafür, wie Unternehmen ihre Effizienz durch Implementierung von Multi-Order Picking um bis zu 38 Prozent steigern können.
Coen Mulder, Functional Control Supply Chain Development bei A.S. Watson, verrät, wie: „In unserem Lager hier in Heteren arbeiten wir schon seit mehreren Jahren mit der Voice-Kommissionierung . Unser System basiert auf der Lösung ZetesMedea. Unsere Auftragsbearbeitung ist in drei Ströme unterteilt: Alle Produkte im aktuellen Sortiment, Produkte im Sonderangebot und E-Commerce-Aufträge.“
„Wir arbeiteten eine Zeit lang mit dem Single-Order Picking. Das bedeutete, dass alle Kommissionierkräfte im gesamten Lager unterwegs waren. Wir haben uns mit Zetes zusammengesetzt, um gemeinsam zu überlegen, wie wir die Wege minimieren konnten. Dabei kamen wir zu dem Schluss, dass wir unsere Effizienz um rund 16 Prozent steigern konnten, wenn wir Aufträge kombinierten. Dazu brauchten wir die Unterstützung von Mengenberechnungen, um jeweils das am besten geeignete Transportmittel mitzunehmen (Paletten oder Behälter). Nach einer eingehenden Analyse der Prozesse implementierten wir daraufhin gemeinsam das Multi-Order Picking.“
Jaqueline van Oostrum, Supply Chain and Logistics Project Manager bei A.S. Watson, ergänzt im Zusammenhang mit der Effizienzsteigerung um 38 Prozent: „Zusammen mit den bereits erwähnten Mengenberechnungen für unsere Auftragstransportmittel und der Erweiterung des Voice-Dialogs für das Batch Picking fügten wir auch mehrere Palettenfahrzeuge hinzu. Die maximal mögliche Verbesserung erzielten wir letztendlich durch die Kombination von Anpassungen bei unserer Software und .den Geräteeinstellungen. Ein wichtiger Faktor war zudem das Engagement aller Mitarbeiter.“
Das Multi-Order Picking für das aktuelle Sortiment hat mit einer beeindruckenden Effizienzverbesserung um 38 Prozent alle Erwartungen übertroffen. Jaqueline van Oostrum, Supply Chain and Logistics Project Manager.
„Zusammen mit minimalen Wegen können wir mit dem Multi-Order Picking zusätzlich Zeit einsparen: zum Beispiel, weil sich das Personal nicht mehr ins Gehege kommt und unnötig in den Lagergängen herumstehen und warten muss. Im Rückblick auf dieses Projekt stellen wir fest, dass unsere Implementierung des Multi-Order Picking für das jetzige Sortiment mit seiner beeindruckenden Effizienzverbesserung um 38 Prozent alle Erwartungen übertroffen hat. Die durchschnittliche Anzahl der kommissionierten Verpackungen pro Stunde ist in diesem Auftragsstrom von 90 auf 125 gestiegen. Angesichts dieses Erfolgs haben wir Multi-Order Picking auch für einen Teil der Produkte im Sonderangebot eingeführt. Unser Ziel sind dabei ähnliche Verbesserungen in diesem zweiten Auftragsstrom“, schließt Jaqueline van Oostrum.