An interview with Pascal Longchambon, identification and traceability expert at Zetes, who talks about the current state of traceability in the phytosanitary sector
Could you give us a quick summary of the benefits of traceability in the phytosanitary sector?
Let's start from the premise that you can't have an efficient, modern traceability system without an automatic data carrier (barcode or data matrix/QR code, RFID chip) to ensure fast, reliable data collection. This carrier (mandatory for the product ID) has evolved to be enriched with relevant information in two key areas:
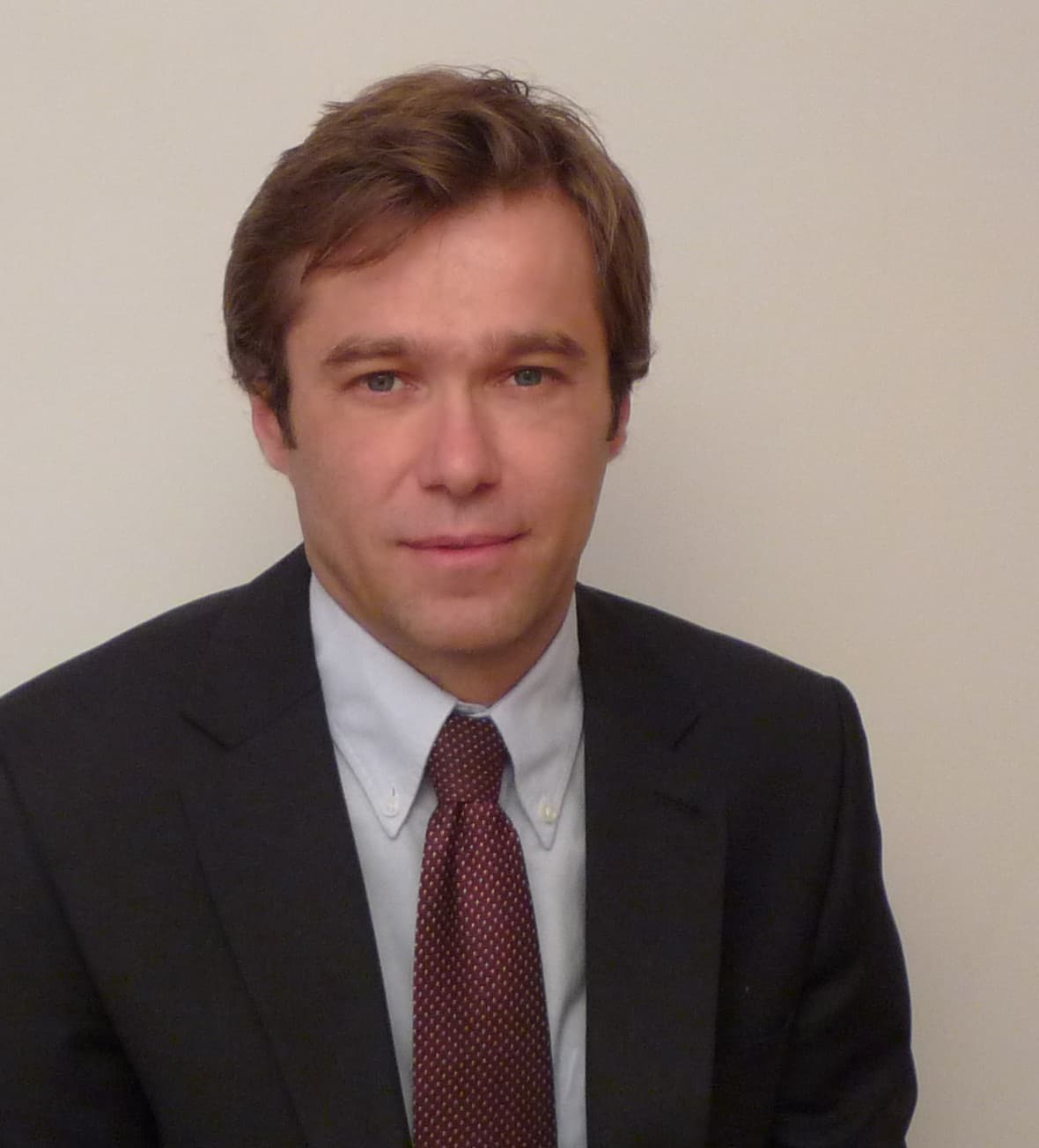
- The addition of contextual production data (Batch No., Expiry date, etc.), for automatic checking of this information at each stage of collection.
- The addition of a unique identifier for a particular product reference (commonly called ‘serialization’), to allow unit traceability (product-level granulometry).
These developments, already tried and tested in other markets, are governed by the CRISTAL standard in the phytosanitary sector. The benefits are tremendous: digitalisation of production, visibility and monitoring of flows in the supply chain, guaranteed authenticity, etc.
What changes must organisations implement to ensure compliance with the standard in their sector?
The impact is significant, because contextual identification requires the ability to print data carriers at the time of packaging, i.e., online. In other words, the automatic identifier is going from a static state to a dynamic state on two levels:
- Batch level
- Product level (serialization) per batch.
The changes can be viewed in two ‘dimensions’. Vertically, all the partners are involved: scheduling, line operation, communication with the peripherals (read/write), execution tasks, and of course the batch reports, their cloud-based storage, and links with the authorities where appropriate. Horizontally and at low level, the line must be managed globally: automated identification processes become communicating, interdependent, and above all collaborative with the environment, from the primary unit to the pallet.
To achieve this, an efficient, proven, and resilient solution is essential, providing many benefits: all processes are monitored, line operation becomes simple and secure, the standard is observed with no impact on performance, and traceability finds a new dimension.
How is the sector doing on the application of the standard?
We work with major players in the sector, each with their own strategies and implementation timetables. The phases are often progressive (serialization and then aggregation). Our pragmatic approach, developed through long experience, gives us a vast capital of standard processes to offer.
From the data source to its execution in a strongly automated environment, the aim is to digitise production in a way that is perfectly faithful to the physical movements. Our customers are always surprised by how easy it is to use a solution they expect to be complex.
What advice would you give to companies that want to choose a serialization/aggregation solution?
A site audit is essential.
This type of solution requires a combination of many areas of expertise corresponding to each “stage” of the process information chain (from sequencing/cloud-based data storage to the physical presence of the product in the workshop). The chosen partner must have significant experience capital, to best guide the implementation procedures, in particular via a detailed analysis report containing all the mandatory prerequisites, the chosen architecture, and the inherent operational changes (from operator level to administrator level).
Can you explain the role of aggregation in the traceability process, and how it benefits the company?
With aggregation, a single “parent” identifier (that of the container) can be used to find all the “child” identifiers (those of the contents). During the consultation, and especially transfers (of location or property), these links can therefore multiply collection speeds by ten by avoiding re-reading at the bottom of the hierarchy. When production is aggregated on the box and pallet levels, a simple reading of the pallet number can locate hundreds or thousands of primary packaging identities. Although this process is often only recommended, it turns out to be almost mandatory to apply it for the sake of productivity all along the supply chain.
What does Zetes offer to help companies in the sector achieve compliance?
As mentioned, in the context of the ‘dynamisation’ of identification, the use of a dedicated execution solution is unavoidable. Offering this type of solution requires diverse skills, which must be made interoperable. These include: transactional IT (exchanges with information systems), management and supervision IT (web), industrial IT (HMI, communication, data formatting and analysis), real-time collaborative and connected automation. The company backs up its ZetesAtlas solution with all these skills, including the design and installation of identification stations (two design offices). This is a fundamental and reassuring point for our customers (and for us): a single point of contact for analysis, implementation, and support, over the entire technical scope.
When confronted with the challenge of dynamic identification, many tools, architectures, and approaches will become obsolete. With its maturity, flexibility, resilience, and unique management of low-level unit execution, ZetesAtlas can guarantee an efficient, independent, and scalable environment.
Remember also that ZetesAtlas is one component of the Zetes Supply Chain solution portfolio. In addition to its proven expertise in the field of identification, Zetes has both vertical skills, with expertise of execution processes, technologies, and integration with business software, and horizontal skills, in providing visibility and traceability systems for supply chain processes in collaborative and real-time mode, from manufacture to the end consumer. These characteristics make Zetes a unique player in the EMEA market, with its ability to offer secure digitalisation of supply chain processes and to guarantee optimum traceability, whether upstream, downstream, internal, or global.